Dans l’industrie il est fréquent de devoir trier des produits selon un ou plusieurs critères (forme,couleur, poids…). À l’image de ces problématiques, on propose ici de concevoir et de réaliser une trieuse de M&M’s selon leurs couleurs.
Notre équipe de 4 étudiants en EI2 est composée de Victor et Clément qui se sont chargés de la conception et la réalisation mécanique du système (réalisation des pièces sous SolidWorks , impression 3D des différents éléments, usinage avec la Charly Robot…) et 2 étudiants (Alexis et Maël) se sont chargés de la partie électronique et programmation (branchements à L’Arduino, commande des deux servomoteurs, récupération des données du capteur de couleur et infrarouge,…). Les deux sous-groupes ont travaillé en parallèle pour finalement fusionner leur travail afin de réaliser la trieuse de M&M’s.
Nous avons été accompagnés pour ce projet par deux professeurs : Mr Rémy Guyonneau et Mr Franck Mercier.
Présentation du projet :
Les différentes pièces composant notre trieuse sont :
–L’Entonnoir : Présent tout en haut de la trieuse, c’est là où on intègre les M&M’s.
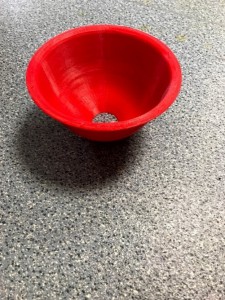
-Le « Porte-FeedWheel » : Pièce centrale de la trieuse, elle est composée d’un petit entonnoir sur le dessus, d’où sortent les M&M’s provenant de l’entonnoir principal, d’espaces vides pour le côté esthétique afin d’apercevoir les M&M’s qui tombent, ainsi qu’un espace en bas pour intégrer les capteurs et la pièce « FeedWheel »
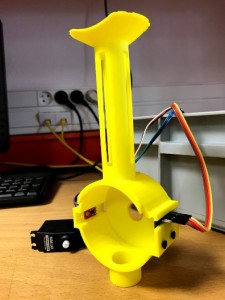
-Le « FeedWheel » : Pièce ronde comprenant 4 cavités dans lesquelles un seul M&M’s peut rentrer. Un moteur à rotation continu est fixé à l’arrière du FeedWheel.
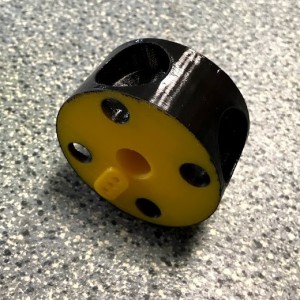
–Un capteur infrarouge : Fixé dans le « Porte-FeedWheel », il permet de détecter les erreurs d’approximations du moteur à rotation continu afin d’ajuster un angle correct.
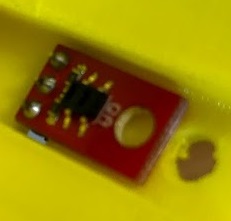
–Un capteur de couleur : Fixé également dans le « Porte-FeedWheel », il permet de détecter la couleur du M&M’s correspondant.
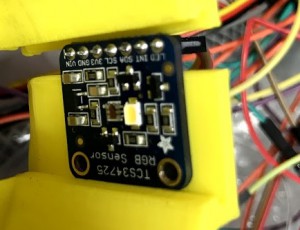
-Le « Tuyau principal » : Directement relié au « Porte-FeedWheel », d’où sortent les M&M’s, collé à un servomoteur. Un angle spécial est appliqué à une couleur précédemment détectée.
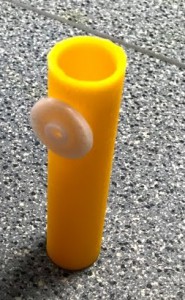
-Le « Séparateur » : Pièce servant de lien entre le tuyau principal et les tuyaux secondaires. La forme du dessus est prévue pour la circulation du tuyau principal. Il comprend 6 trous, chaque trou correspond à une couleur.
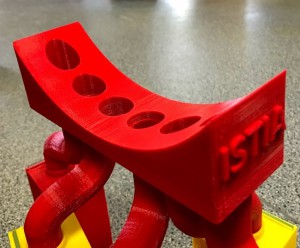
-Les « Tuyaux secondaires » : Ils sont au nombre de 6 et servent de liaison entre le séparateur et les bocaux.
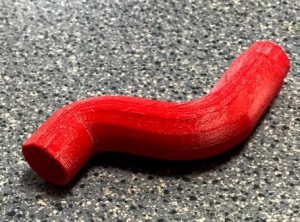
–Les bocaux : Ils sont également au nombre de 6 et sont les pièces de présentation des M&M’s finalement triés.
Ils sont reliés aux tuyaux secondaires correspondants et possèdent chacun une vitre transparente découpée avec le « Charly Robot ».
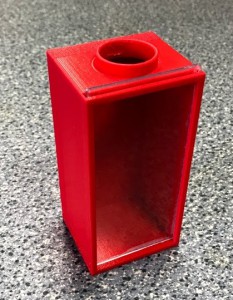
Au final nous avons assemblé toutes ces pièces et cela nous a donné une belle trieuse !
Les différentes étapes de notre projet :
Premièrement, nous avons établi en commun au brouillon une structure qui nous paraissait correct pour la partie mécanique et pour la partie programmation, tout en s’inspirant de même type de trieuses déjà existantes.
Une fois la structure plus ou moins établi au brouillon, nous séparons nos travaux en 2 groupes :
Après l’assemblage de ces pièces toujours sur SolidWorks, ce groupe passa aux impressions en 3D avec les imprimantes Raise3D et Makerbot.
En parallèle, pour les bocaux en bas de la structure, ce groupe réalisa un usinage grâce à la Charly Robot avec du plexiglas afin de créer une vitre transparente permettant de voir les M&M’s.
L’autre groupe se chargeait de la programmation de l’ensemble des composants électronique, à savoir : deux capteurs (RGB et Infrarouge) et deux moteurs (à rotation continu et servomoteur).
Ainsi nous avons commencé la programmation de chaque composant indépendamment pour prendre en main la programmation Arduino plus facilement.
Une fois chaque programme fini, nous les avons rassemblés en un et organisé la structure de notre programme final. De nouveaux composants se sont ensuite ajoutés comme l’écran LCD, le bouton ou l’utilisation d’un capteur IR pour positionner le moteur à rotation continue.
Problèmes rencontrés
Nous avons eu pas mal de problèmes au cours de notre projet.
Dès le départ nous ne savions pas par où commencer, comment se partager les tâches etc. Par la suite, nous avons commencé à imaginer le projet, il était difficile de mettre en commun nos idées. Lorsque nous sommes passés sous Solidworks, de nombreux bugs nous ont posé problème.
De plus, des pièces que nous avions modélisées puis imprimées se sont avérées ne pas être aux bonnes dimensions ou bien avec trop peu de jeu pour assembler les pièces. La couleur jaune de la pièce « FeedWheel » fut embêtante pour l’étalonnage des couleurs de bonbon. Cela a été résolu en aspergeant cette pièce avec une bombe de peinture noire.
Le problème majeur était surtout les pannes d’imprimante 3D qui nous ont beaucoup ralenties.
En programmation, il y a également eu quelques soucis. Par exemple, pour trouver la documentation de certains composants comme pour le capteur couleur ou l’écran LCD, la documentation était fausse.
Nous avons aussi rencontré des problèmes avec le câblage qui devenait illisible et problématique. Il était donc nécessaire de remettre des fichiers dans la racine du logiciel Arduino. Il a aussi été difficile d’étalonner chacune des couleurs des M&M’s.
Conclusion
Pour conclure, nous voulons absolument remercier nos tuteurs Mr Mercier et Mr Guyonneau pour toute l’aide apportée au cours de ce projet.
Pour nous, ce projet fut une grande expérience dans tout ce qui est du travail en groupe, de l’innovation, de la pratique…
Voir le projet grandir au fur et à mesure des séances nous a aussi motivé pour avancer et perfectionner le projet au maximum.
Merci à vous, chers lecteurs de vous être intéressés à notre projet.
Victor B, Clément C, Alexis G, Maël C