Présentation du projet
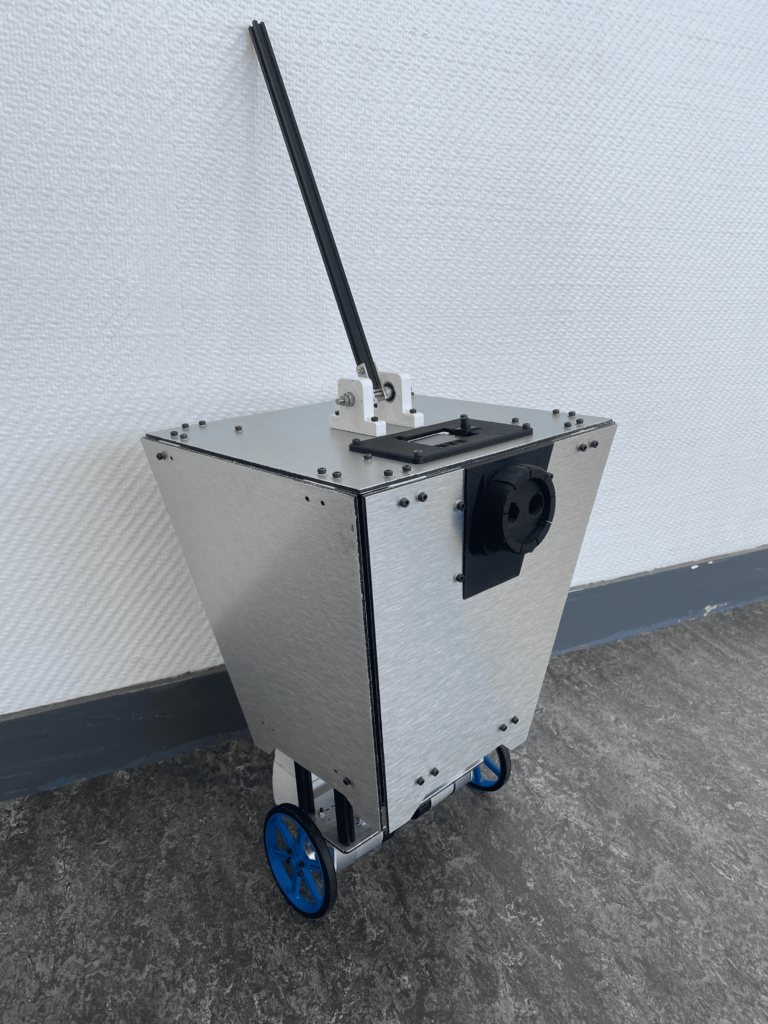
Bonjour nous sommes Ewan BUDOR et Antoine HOMMETTE deux étudiants en deuxième année à Polytech Angers. Et aujourd’hui nous allons vous présenter Le projet Double Pendule – Balancing Bot.
Notre projet consiste à concevoir et fabriquer la partie mécanique d’un robot basé sur le principe de fonctionnement d’un segway pour maintenir son équilibre. En ajoutant une extension pour en faire un double pendule.
Intro
Nous avons choisie de diviser notre travail en 6 étapes. Et aujourd’hui nous allons vous les expliquer :
- Schéma fonctionnel
- Recherche des composants
- Choix du design général
- Conception des pièces
- Fabrication des pièces
- Montage du robot
Schéma fonctionnel
La première étape a été de créer un schéma fonctionnel du robot. Nous avons identifié les composants nécessaires pour le fonctionnement du robot. Ensuite, nous avons relié ces composants pour représenter le fonctionnement du robot avec les flux d’informations et d’énergie. Ce schéma a été soigneusement élaboré pour éviter les erreurs et gagner du temps. Nous avons présenté plusieurs versions de ce schéma à M. Mercier, qui nous a donné des conseils pour l’améliorer.
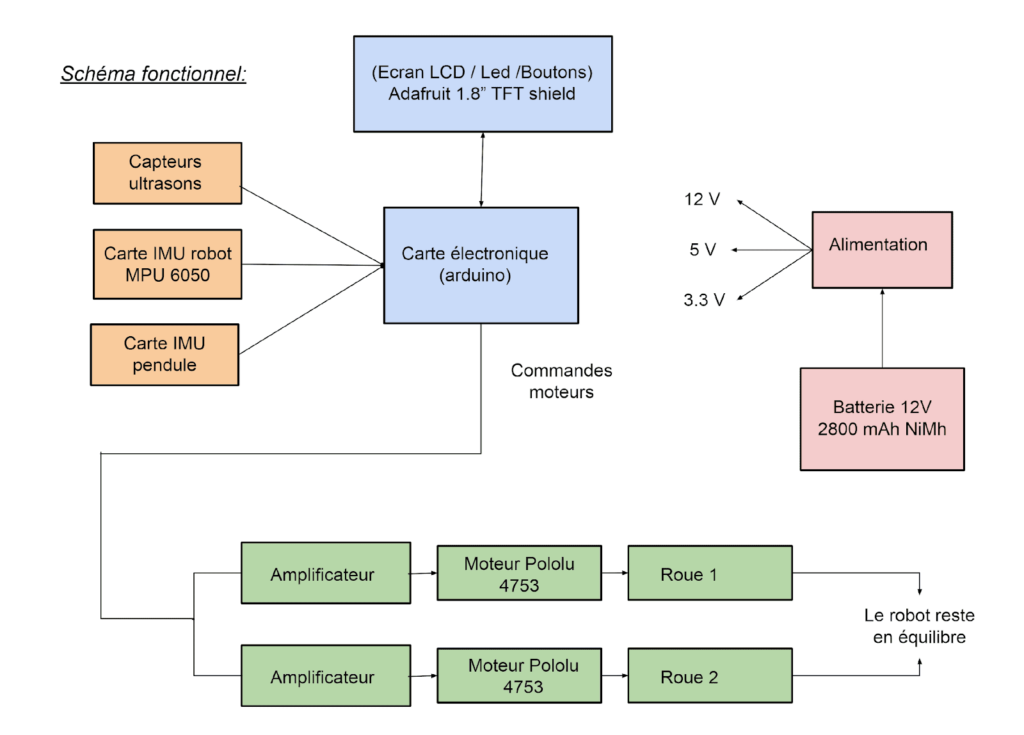
Recherche des composants
La deuxième étape était la recherche des composants nécessaires pour notre robot. Nous avons trouvé la plupart des éléments à Polytech, grâce à M. Mercier qui nous a fourni les composants électroniques essentiels. Étant donné que le niveau en électronique et codage était trop élevé pour nous. Et aussi car nous ne nous occupions pas de la partie programmation du robot.
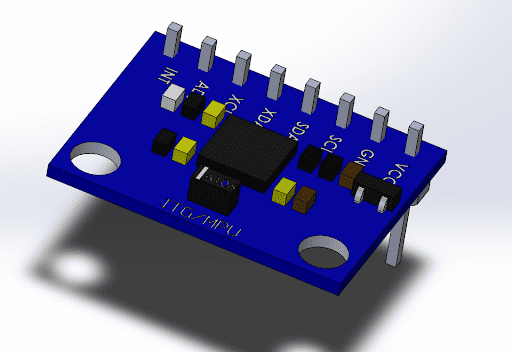
Ensuite, nous avons recherché les modèles 3D dans des bibliothèques en ligne telles que GrabCAD et Pololu pour planifier les dimensions et l’assemblage des pièces. Cependant, cette étape s’est révélée difficile et a pris beaucoup de temps en raison de la complexité à trouver les modèles 3D appropriés.
Choix du design général
La troisième étape a été de réfléchir à l’esthétique générale que nous souhaitions donner au robot, avec l’objectif qu’il soit attrayant pour le grand public. Nous avons recherché des idées sur Internet en examinant des robots déjà existants, mais nous n’avons pas trouvé ce que nous recherchions. Nous avons donc élargi notre recherche à d’autres supports tels que les films et les jeux vidéo, où l’esthétique est plus importante. Finalement, nous avons trouvé notre principale source d’inspiration dans le jeu Borderland.
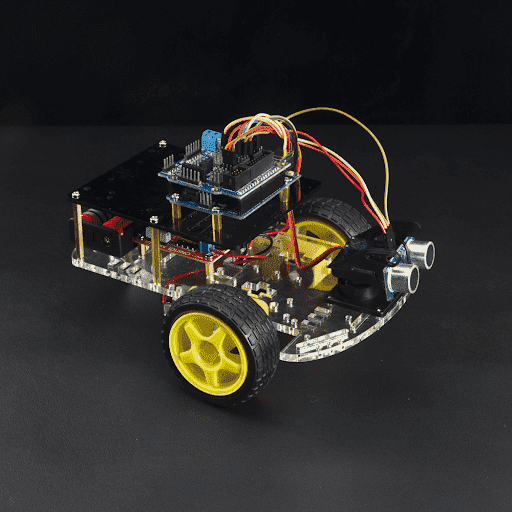
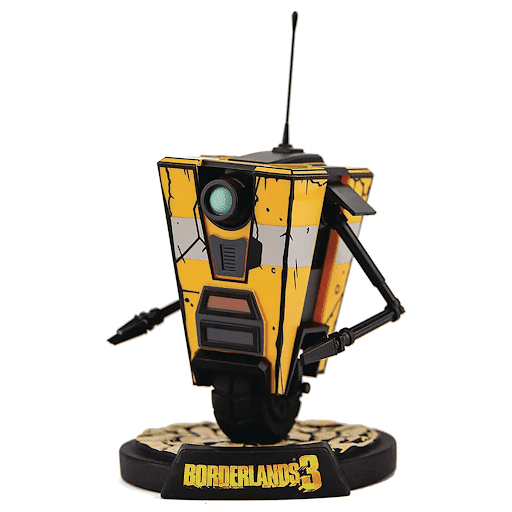
Nous avons apporté quelques modifications pour adapter le design aux composants que nous avions. Par exemple, nous avons remplacé le modèle à une roue par un modèle à deux roues et utilisé l’antenne comme second pendule. Ensuite, nous avons simplifié le design avant de commencer la conception assistée par ordinateur (CAO).
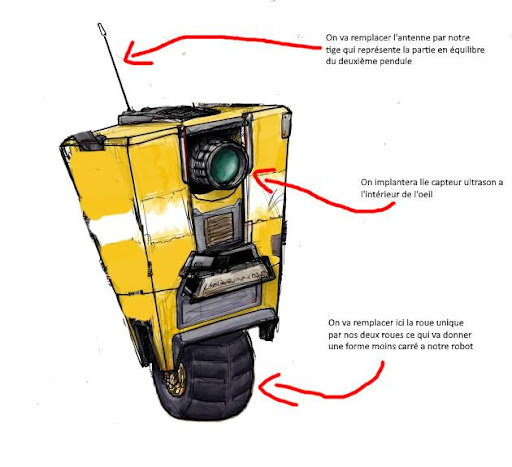
Conception des pièces
La quatrième étape est la conception des pièces, nous avons créé chaque pièce en 3D pour relier la conception à la réalité. Nous avons utilisé SOLIDWORKS, un logiciel de CAO, pour créer les pièces en tenant compte des dimensions et des contraintes de fabrication. Nous avons importé les pièces existantes dans un assemblage pour visualiser notre travail.
En partant de la base des pièces existantes, nous avons conceptualisé la structure du robot en utilisant des poutres profilées en aluminium pour soutenir la partie supérieure. Nous avons ajouté des plaques en dibond pour renforcer la structure et fournir de l’espace pour les composants. Nous avons laissé plus d’espace que nécessaire pour permettre d’éventuelles modifications ou ajouts futurs.
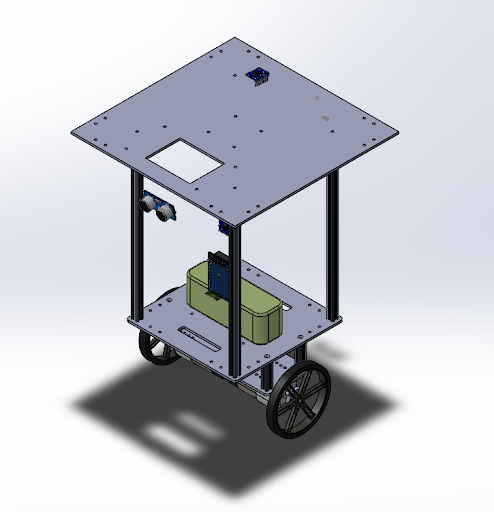
Ensuite, nous avons créé les pièces qui constituaient la majeure partie de l’esthétique extérieure du robot. Nous avons utilisé du dibond pour les plaques du carénage et des équerres en plastique imprimées en 3D pour les fixer, en donnant à notre robot la forme d’une pyramide inversée. Nous avons conçu un carénage qui englobe la majorité du robot.
Enfin, nous avons réalisé les finitions. Nous avons créé des supports pour le pendule, avec des roulements à billes pour l’axe de rotation. Nous avons fixé une partie du pendule à l’aide de plaques métalliques et ajouté une centrale à inertie. Nous avons également créé un cache pour l’écran, en veillant à ce que l’accès aux boutons soit facilité. Des supports ont été prévus pour les capteurs à ultrasons, avec des designs différenciés pour l’avant et l’arrière du robot. Nous avons fixé la batterie en bas de la coque avec des attaches en plastique.
Ces étapes de conception nous ont permis de concrétiser notre robot en prenant en compte à la fois l’aspect esthétique et fonctionnel.
Fabrication des pièces
La cinquième étape est la fabrication des pièces du robot, pour cela nous avons utilisé plusieurs machines mises à notre disposition, notamment une machine de découpe CNC pour usiner les plaques en dibond. De plus, nous avons eu recours à des imprimantes 3D afin de créer des pièces plus complexes, telles que les supports de carénage et de pendule. En plus, nous avons utilisé plusieurs outils du fablab tels qu’une perceuse, une scie à métaux, des étaux, des pinces et un étau.
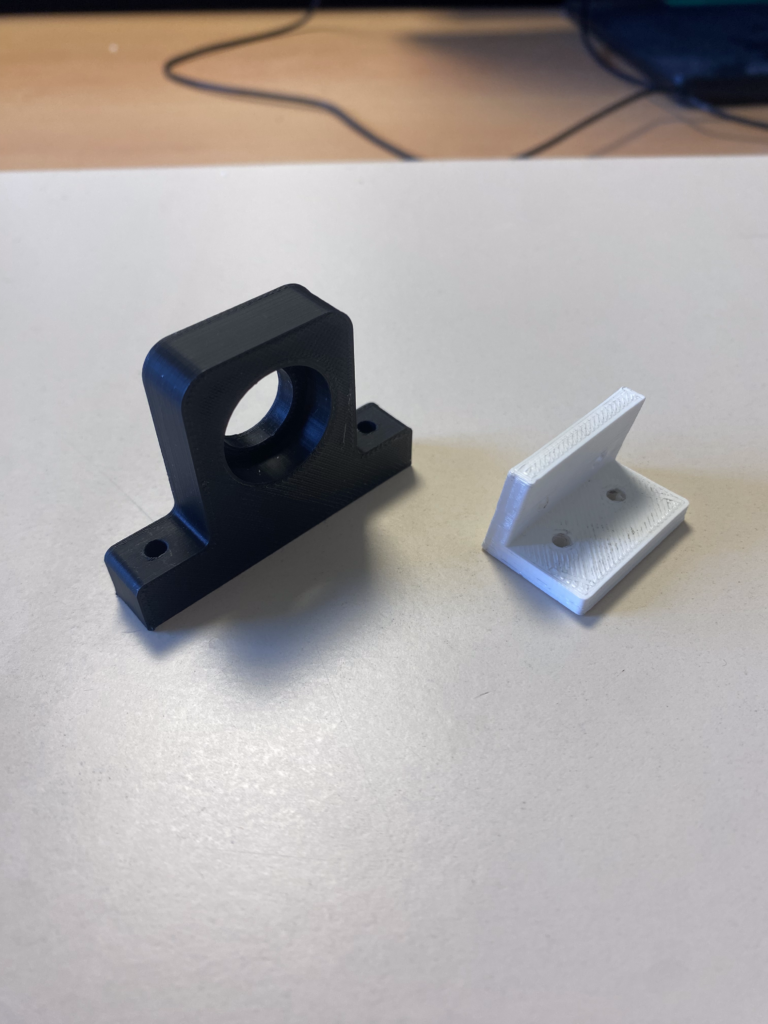
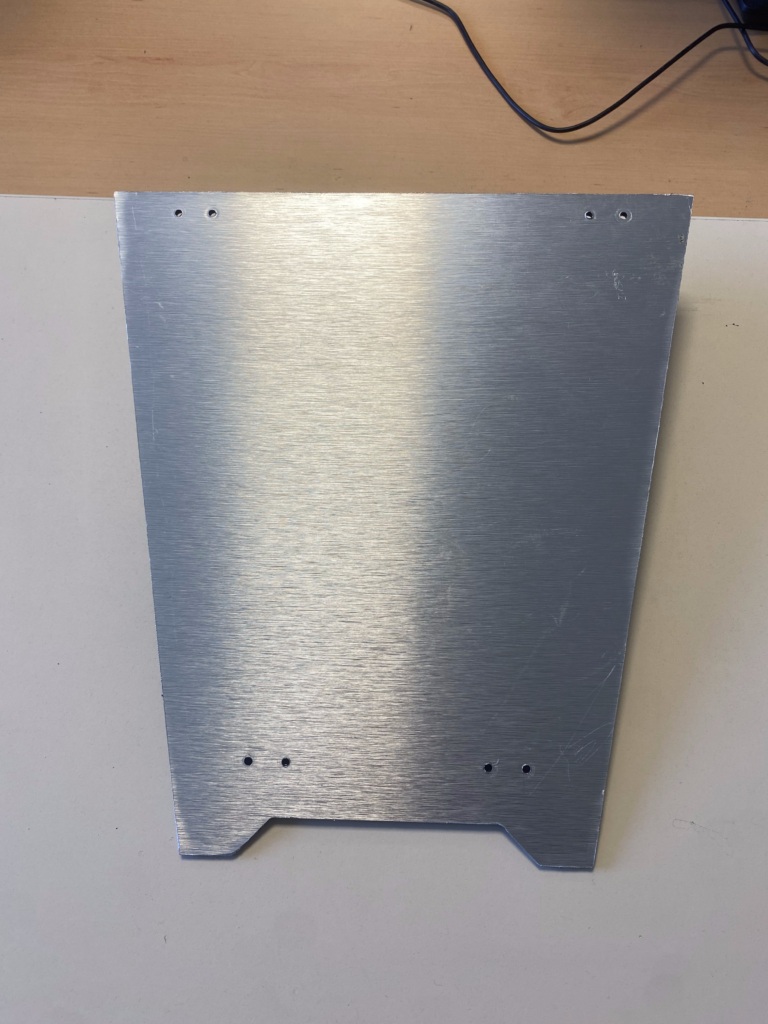
Montage du robot
La dernière étape est le montage du robot. Pour pouvoir monter le robot plus rapidement pendant la création des pièces, nous assemblions le robot. Nous avons commencé par la partie inférieure, en utilisant les pièces du châssis pour former une base solide. Nous avons rencontré quelques différences entre la conception et la réalité, mais nous avons pu apporter rapidement des ajustements. Ensuite, nous avons monté la structure, les premiers composants internes et les carénages, malgré quelques problèmes de conception. Nous avons réussi à assembler toute la partie inférieure du robot.
Nous avons également monté le pendule et son support, en testant différentes pièces jusqu’à trouver un assemblage qui permettait au pendule de se déplacer librement tout en restant aligné.
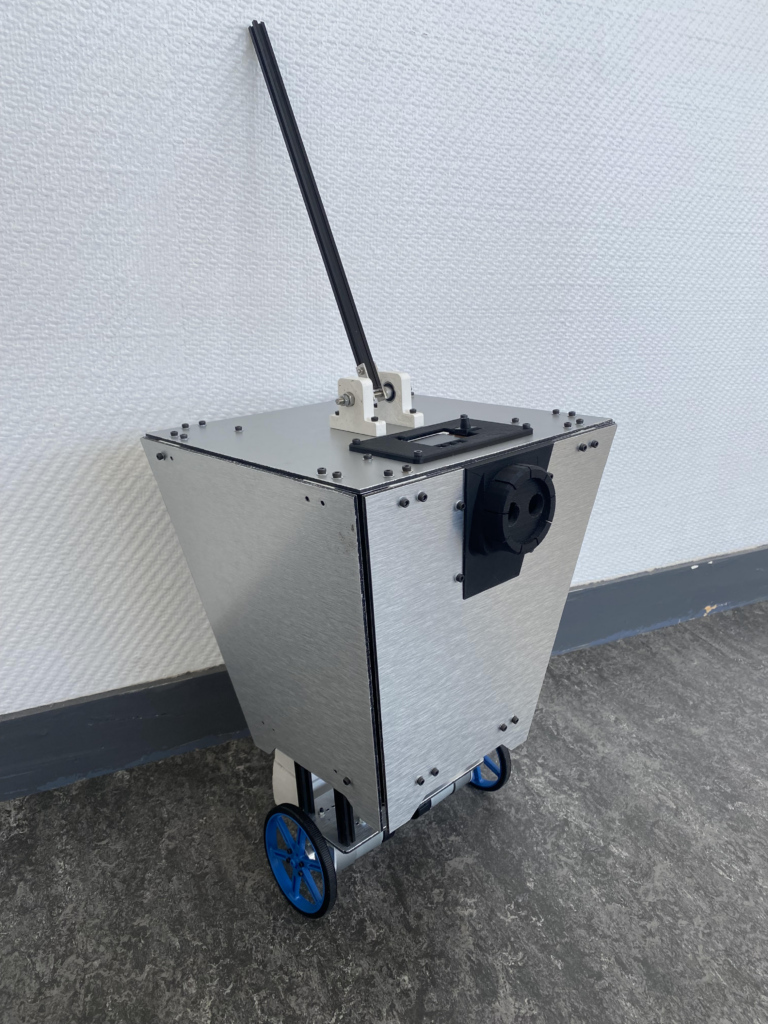
Enfin, nous avons fixé le pendule sur le sommet du robot et installé les derniers composants tels que le cache d’écran avec la carte et le cache, ainsi que les capteurs à ultrasons.
Nos avis sur le projet.
« Malgré une légère frustration de ne pas pouvoir voir notre robot en fonctionnement pour l’instant, j’ai réellement pris plaisir a effectuer ce projet. Je suis devenu plus autonome et j’ai appris énormément. »
Ewan BudoR
« Ce projet a été une expérience incroyablement enrichissante et stimulante, malgré mes réticences initiales. J’ai développé un réel engouement pour la conception et la réalisation du robot. »
Antoine HOMMETTE
Si cet article vous a plu je vous invite à venir lire notre rapport de projet qui vous permettra d’en apprendre plus sur le projet Double Pendule.
Polytech Angers – Projets PEIP2
Proudly powered by WordPress