Introduction à l’éolienne
Notre consommation d’énergie a atteint un point tel que l’épuisement des sources d’énergies fossiles est imminent. C’est pourquoi, nous devons nous concentrer sur le développement des énergies renouvelables, notamment l’énergie éolienne.
Le vent est une des premières énergies utilisées par l’Homme, que ce soit pour la navigation ou encore faire tourner les moulins. Aujourd’hui, c’est une nouvelle façon de produire de l’électricité. Le processus consiste à transformer l’énergie cinétique du vent en énergie mécanique grâce à la rotation d’un arbre. Cette énergie va alors devenir électrique grâce à un générateur électrique.

En ce qui concerne le fonctionnement, nous allons l’expliquer simplement. Tout d’abord, le vent, suffisamment fort, fait tourner les pâles de l’éolienne, ce qui entraine la rotation du moyeu et de l’arbre principal. Cet arbre passe ensuite dans un multiplicateur qui va augmenter considérablement sa vitesse de rotation. La vitesse de rotation doit être élevé en sortie afin de faire démarrer l’alternateur grâce à une vitesse du rotor assez élevé. Par la suite, l’alternateur génère de l’électricité grâce à un système d’électro-magnétisme. Ce courant électrique est alternatif, il doit être transformé dans le transformateur, puis il rejoint le réseau électrique grâce aux câbles.
Comment fabriquer une eolienne ?
Le materiel
Pour fabriquer notre éolienne nous avons choisi de faire une méthode utilisant beaucoup de matériel récupéré. Il a aussi fallu commander quelques éléments notamment pour le circuit électrique.
Liste de matériel
- Moteur continu
- Régulateur
- Redresseur de tension
- Condensateur
- Carte électronique
- Planche de bois
- Mat en bois
- Pied de parasol
- 3 Pâles imprimées en 3D
- Moyeu imprimé en 3D
- Support moteur imprimé en 3D
- Vis
Etape 1 : Le circuit electrique
Nous avons commencé par réaliser le circuit électrique car ce sont les premiers matériaux que l’on a reçu. Nous avons utilisé une carte en métal pour poser tous nos composants, puis nous les avons brasés ensemble, en respectant attentivement le circuit suivant.

Dans un premier temps nous avons intégré la sortie du moteur sur la carte. Puis nous avons positionné le pont de redressement et brasé les branches du moteur à celles de courant alternatif du redresseur.
Dans un second temps, nous avons brasé la branche + du redresseur avec la branche + du condensateur. Et nous faisons de même avec les branches -.
Puis nous brasons la branche + du condensateur à l’entrée du régulateur, et la branche – à la masse.
Finalement, nous relions la branche de sortie du régulateur au la VCC du connecteur USB femelle 5V. Et la masse du régulateur à la masse du connecteur.
Etape 2 : conception du support du circuit
Pour assembler notre planche à notre rotor, nous choisissons de réaliser un support qui retiendra le moteur et le fixera à la planche. Cette planche est elle-même fixée au mât. L’arbre du moteur sera lui lié au moyeu.
Pour ce faire, nous utilisons SOLIDWORKS afin de créer un support ressemblant à l’image ci-contre.
Le support dépend de la taille de notre planche, de la taille du moteur et de la longueur de l’arbre. Nous avons aussi extrudé des cercles du diamètre de nos vis à bois pour faciliter la fixation à la planche. Et le tour est joué.
etape 3 : conception des pâles et du moyeu
Pour faire le rotor, c’est à dire les pâles et le moyeu, nous avons utiliser l’imprimante 3D. Or il a fallu d’abord faire la conception grâce à SOLIDWORKS. Nous avons cherché le profil de pâle le plus optimal : le profil NACA 6409. Et nous l’avons reproduis dans le logiciel de conception. Puis avec on balaye cette figure pour avoir une pâle plus fine à son extrémité et on la lisse.


Ensuite il nous fallait en imprimer 3 : nombre de pâles idéal qui observe le meilleur rendement et qui évite d’avoir trop de perturbations entre les pâles.
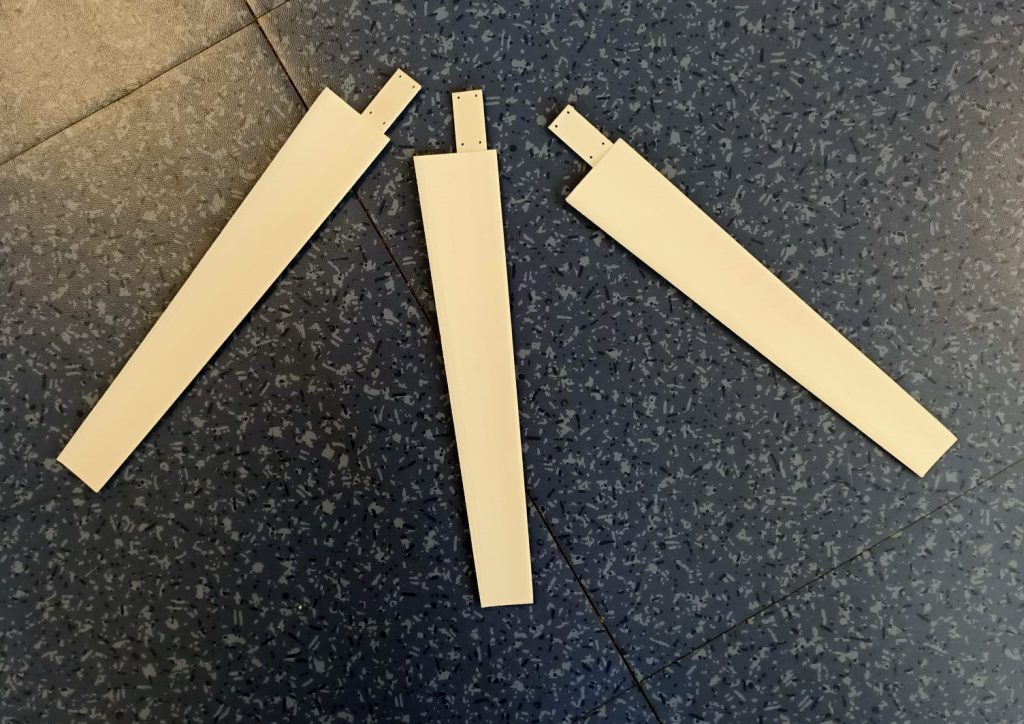
Etape 4 : Decoupe du bois
La découpe du bois fut plutôt simple. Il nous fallait une surface plane pour assembler notre mât et la planche. Alors on a découpé notre mât par la moitié sur une longueur de 14 cm, ce qui correspond à la largeur de la planche. C’est cette planche qui permettra de guider l’éolienne et de l’orienter face au vent.
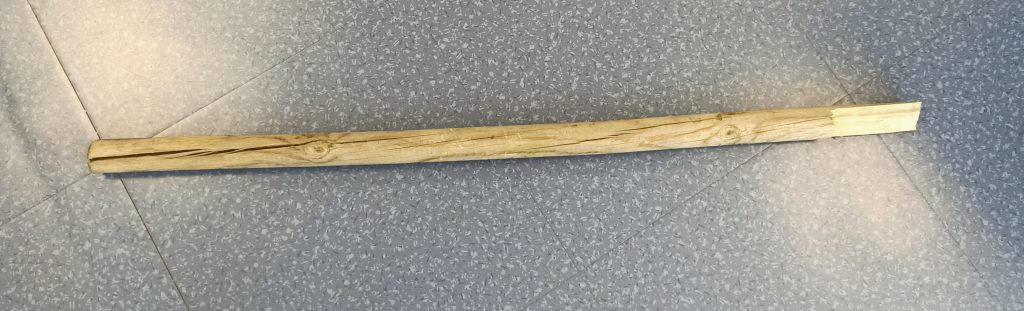
Etape 5 : assemblage
L’assemblage se fait lui même en plusieurs étapes : il faut mesurer et percer le bois, visser la planche au mat, visser le support à la planche et lier le rotor au moteur.
Ainsi nous avons d’abord percé la planche puis nous l’avons vissée au mât.
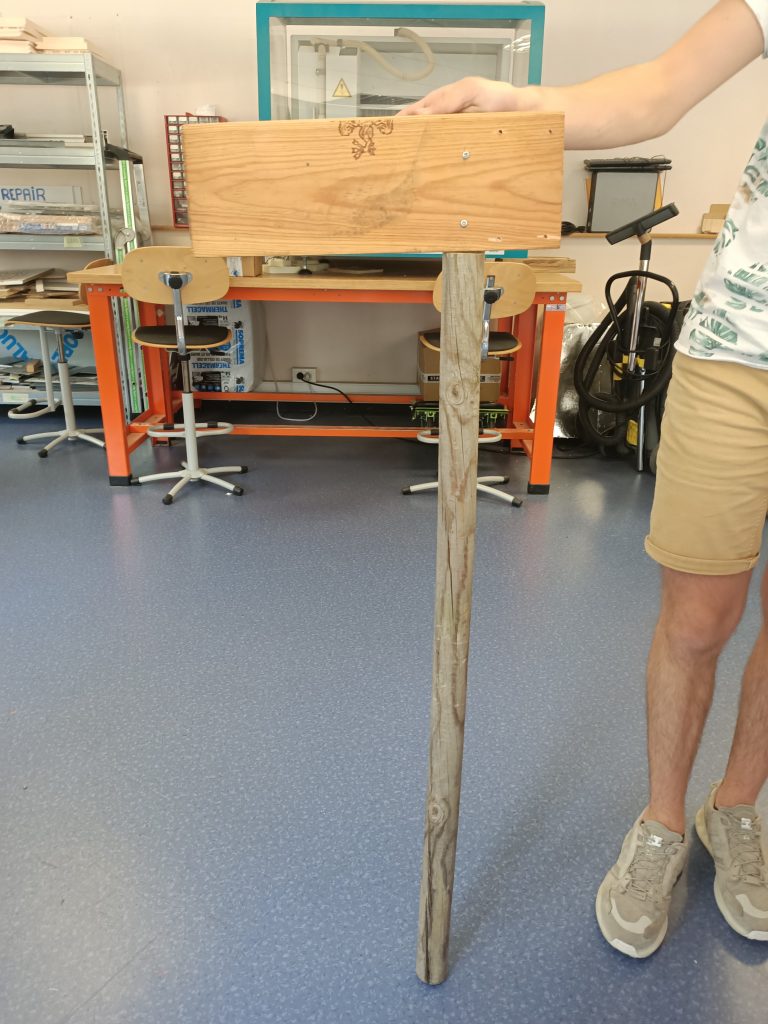
Puis nous avons lié les pâles au moyeu avec de la colle forte. Et de la même manière nous avons fixé le moyeu à l’arbre. Afin que ce dernier soit entraîné par la rotation des pâles.
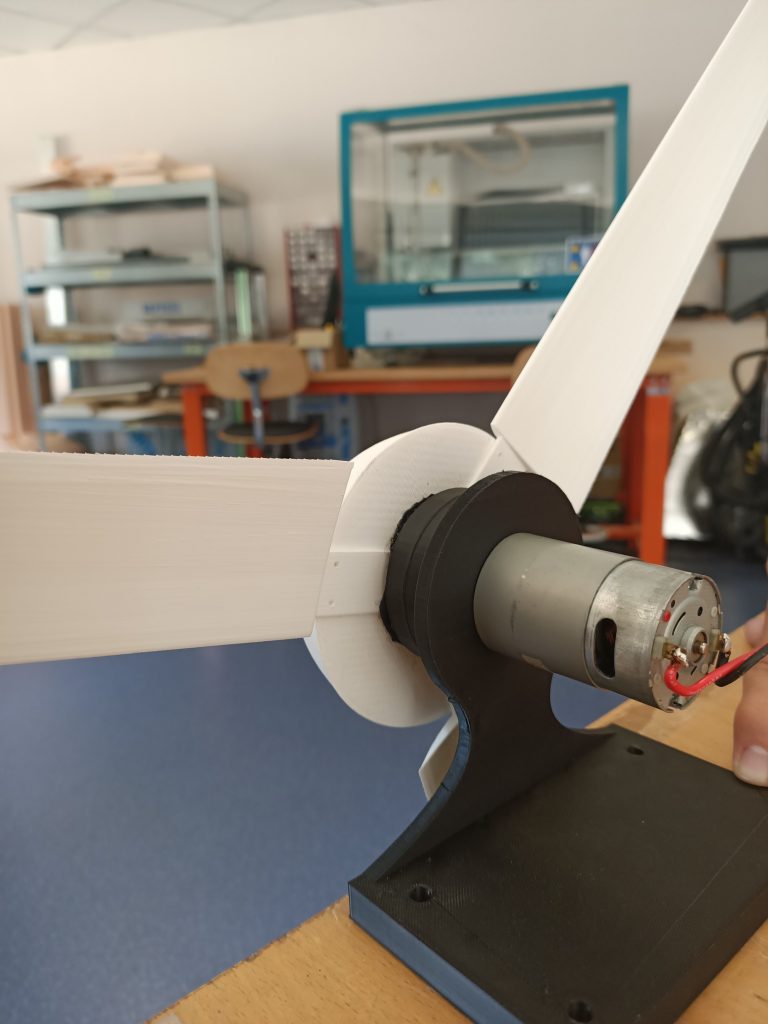
Enfin nous avons vissé le support à la planche, à l’aide de 4 vis et de 4 écrous.
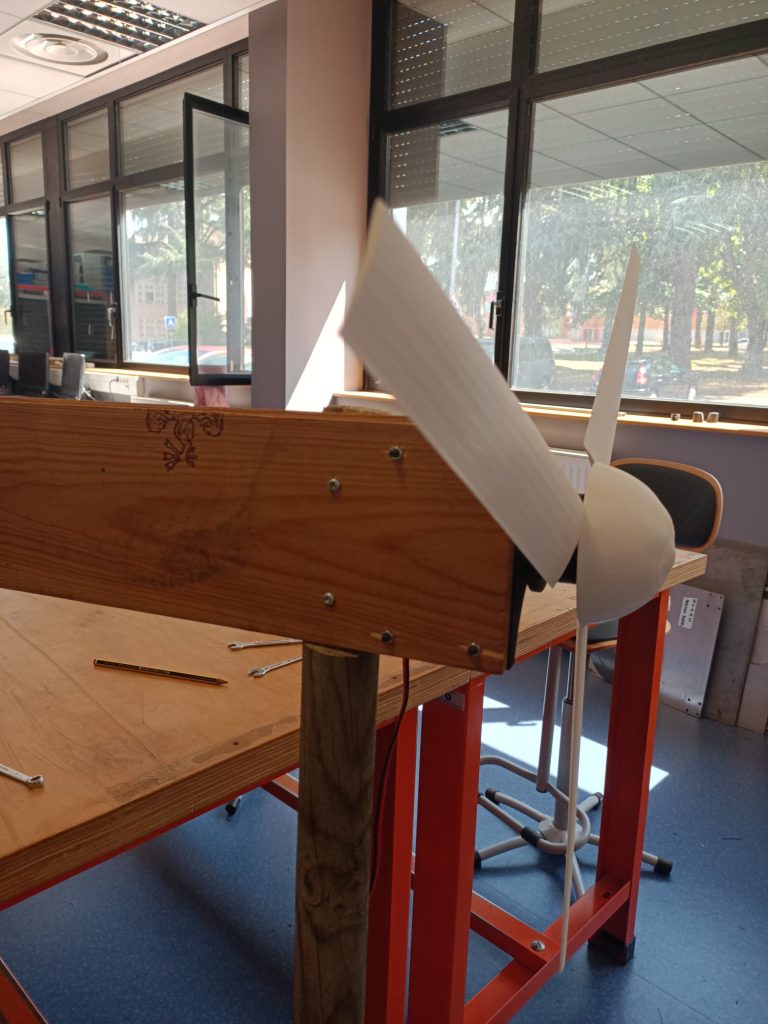
Conclusion
Pour conclure, cette éolienne low-tech est plutôt rapide à faire, elle n’utilise pas beaucoup de matériaux neufs mais a un système électrique insuffisant pour charger un téléphone. A notre plus grand regret.
Sean GALLAGHER, Maxime HERBRETEAU, Léane NEVEU