Cher lecteur, Chère lectrice,
Nous sommes trois étudiants en PeiP2-A (deuxième année de classe préparatoire intégrée) à l’école d’ingénieurs Polytech Angers, et c’est à travers cet article que nous allons vous résumer et vous expliquer notre travail de groupe.
Commençons d’abord par nous présenter.
Nous sommes Alexi Schmid, Virgile Siegler et Tanguy Moriceau, âgés de vingt ans et futurs ingénieurs.
Comme annoncé précédemment, nous avons eu le plaisir de travailler tous les trois en groupe durant notre dernier semestre de classe préparatoire, sur un projet de conception. Il y avait beaucoup de choix possibles (vraiment beaucoup) et nous avons choisi de travailler sur la conception d’un carrousel simplifié.
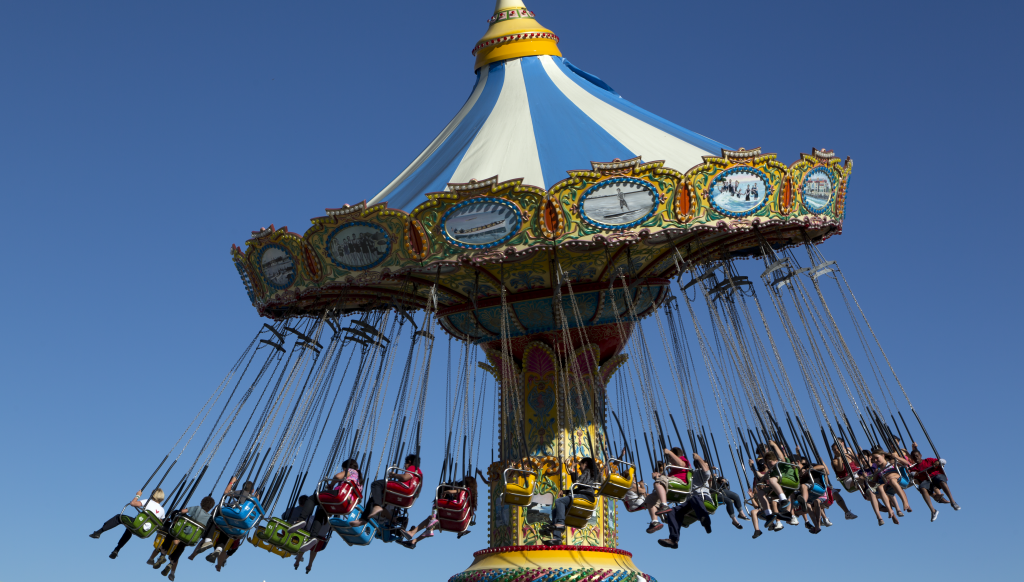
Image 1 : Nous avons travaillé à la conception d’un carrousel comme celui-ci (mais en plus simple parce que là, il y a trop de chaises).
Pourquoi un tel choix ? Nous voulions tester nos capacités et compétences dans des domaines spécifiques. Dans notre cas, ces domaines principaux étaient la résistance des matériaux et l’analyse des systèmes mécaniques (pour plus de précision sur ces sujets, rendez-vous au bas de l’article).
Des modules à l’école nous ont donnés des notions dans ces domaines, mais ce projet de conception n’avait rien à voir avec ce qu’on a fait en cours. Nous étions au maximum en autonomie et devions donc trouver toutes les solutions par nous-mêmes.
Ainsi, ce projet était pour nous un moyen de nous améliorer sur des sujets où nous n’étions pas forcément à l’aise.
1) Présentation du projet et du cahier des charges
L’objectif du projet est clair : concevoir un carrousel simplifié à l’aide de calculs de résistance des matériaux et des notions acquises durant les quatre semestres d’études.
Pour ce qui est du cahier des charges, il y avait différentes conditions à respecter, comme la vitesse maximale de rotation du poteau central (imposée à trente tours par minute), le nombre d’enfants pouvant s’asseoir dans le manège (quatre enfants maximum, tous assis sur des sièges différents et pesant environ quarante kilos chacun) ou même des dimensions de pièces (comme celle du poteau central, qui devait être d’une hauteur de deux mètres).
Enfin, le carrousel devait être le plus léger possible, afin de réduire les coûts matériels.
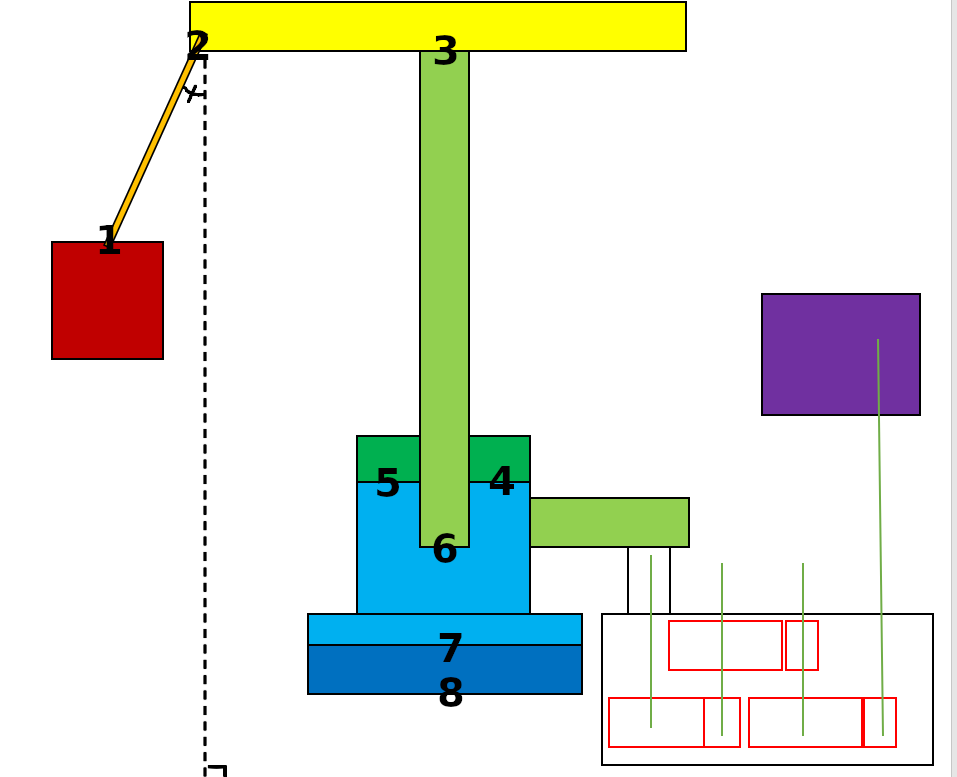
Image 2 : Schéma simplifié du carrousel (en jaune les quatre poutres supérieures, en rouge les sièges, en vert clair le poteau central et la courroie transmettant la rotation, en bleu le châssis, en vert foncé le couvercle du châssis et en violet le moteur, relié au réducteur).
2) Le travail réalisé
Pour réussir ce projet, nous avions deux tâches majeures à faire : la première, était de dimensionner l’intégralité des pièces du manège et de choisir les composants permettant de les lier entre elles. La seconde tâche était de choisir un moteur adapté et de concevoir un réducteur, nécessaire pour réduire la vitesse de rotation du moteur (rappelez-vous que notre manège doit tourner à la vitesse maximale de trente tours par minute !)
Nous avons naturellement commencé par faire un schéma du système à concevoir (voir Image 2), ce qui nous a permis de visualiser le carrousel et de faire ressortir ses points-clés (numérotés en gras sur l’Image 2).
Pour continuer, nous nous sommes engagés sur les calculs des forces appliquées aux quatre sièges. Celles-ci comprenaient la force centrifuge, la résistance à l’air, le poids et les forces radiales et tangentielles. Enfin, nous avons calculé l’angle α, situé entre le câble soutenant le siège et la
perpendiculaire au sol (cet angle est aussi représenté sur l’Image 2).
Cet angle particulier change de valeur suivant la vitesse de rotation du manège. En effet, plus ce dernier tourne vite et plus l’angle α est élevé (car le siège subira une force centrifuge plus forte).
Nous avons donc calculé la valeur de cet angle pour la vitesse de rotation maximale, valant trente tours par minute.
Ainsi, à vitesse maximale, l’angle α vaut 62°.
Grâce aux valeurs des forces précédemment calculées et grâce à cet angle α désormais connu, nous avons mis en place différents torseurs de forces (si cette notion de torseur ne vous est pas familière, je vous renvoie ici pour plus d’explications sur leurs principes), aux points-clés du carrousel.
Avec ces torseurs nouvellement définis, nous avons utilisé le Principe Fondamental de la Statique (que vous êtes censés savoir maîtriser !) aux points-clés du manège, dans le but de déterminer, dans notre repère cartésien (repère tridimensionnel classique, dépendant de trois variables : x pour la longueur, y pour la largeur et z pour la hauteur), les valeurs des forces s’appliquant en ces mêmes points.
En connaissance des différentes forces, nous avons utilisé plusieurs formules issues de notre module de Propriétés et Résistance des Matériaux, pour déterminer les épaisseurs et les diamètres minimaux de pièces composant notre carrousel.
En faisant cela, nous avons aussi respecté une autre contrainte de notre cahier des charges, qui imposait une contrainte admissible de 120 MPa ou de 120 Newtons par millimètre carré (c’est-à-dire que le matériau en question doit pouvoir résister à une force de 120 Newtons, appliquée sur un millimètre carré) pour toutes les pièces.
Par exemple, ce sont avec ces formules que nous avons calculé le diamètre minimal à adopter pour le poteau central. Nous voulions que ce poteau soutienne tout le haut de la structure, mais avec le diamètre le plus faible possible, toujours dans le but de diminuer les coûts de production (il n’y a pas de petites économies !).
Pour continuer avec le poteau central, c’est en calculant son diamètre minimal que nous avons choisi les roulements (à partir d’une documentation issue de constructeurs) pouvant permettre sa rotation au sein de son châssis.
Suite à cela, nous avons de nouveau utilisé le Principe Fondamental de la Statique et les formules de notre module pour déterminer les diamètres intérieur (qui est en fait le diamètre extérieur du roulement défini précédemment) et extérieur adéquats du châssis.
Enfin, nous avons choisi une butée (l’élément se plaçant sous le poteau central, dans le châssis, et permettant la rotation) parmi celles qui nous étaient proposées.
Suite à cela, nous devions choisir les composants permettant de fixer les pièces entre elles, dans des liaisons d’encastrements, en sachant que les composants les plus efficaces pour faire cela sont des vis.
Nous avons donc calculé les forces et les contraintes de cisaillement et de traction (voir au bas de l’article pour plus de précisions) que subiront les vis, dans le but de déterminer leurs caractéristiques.
Celles-ci trouvées, nous avons choisi les vis appropriées (toujours grâce à la documentation) qui permettaient de maintenir le carrousel.
Par la suite, il nous fallait déterminer la courroie et la poulie à utiliser pour transmettre le mouvement de rotation, du réducteur jusqu’au poteau central.
Nous avons facilement choisi ces éléments grâce à nos résultats précédents, à la documentation et aux formules qui nous ont été données par notre professeur encadrant.
Pour finir, nous avons calculé le poids combiné de la poulie et de la courroie, ce qui a achevé la première partie de notre projet de conception.
La seconde partie de notre projet consistait à concevoir le réducteur et nous l’avons commencée en calculant la puissance nécessaire pour obtenir la vitesse de rotation maximale de trente tours par minute.
Après un simple calcul, nous avons trouvé la puissance minimale requise et avons, par la même occasion, choisi le moteur le plus adapté à notre cas de figure.
Ensuite, avec ce moteur, nous sommes passés à la conception du réducteur.
Nous avons calculé le taux de réduction de l’ensemble, c’est à dire le nombre de fois que l’on va réduire la vitesse initiale de sortie du moteur.
Par exemple, si notre moteur tourne à une vitesse de 1600 tours par minute et que l’on impose un taux de réduction de 4 au réducteur, la vitesse de rotation qui sera mesurée après ce dernier, sera de 400 tours par minute.
Avec ce taux de réduction et la documentation, nous avons déterminé qu’il fallait concevoir un réducteur à trois étages.
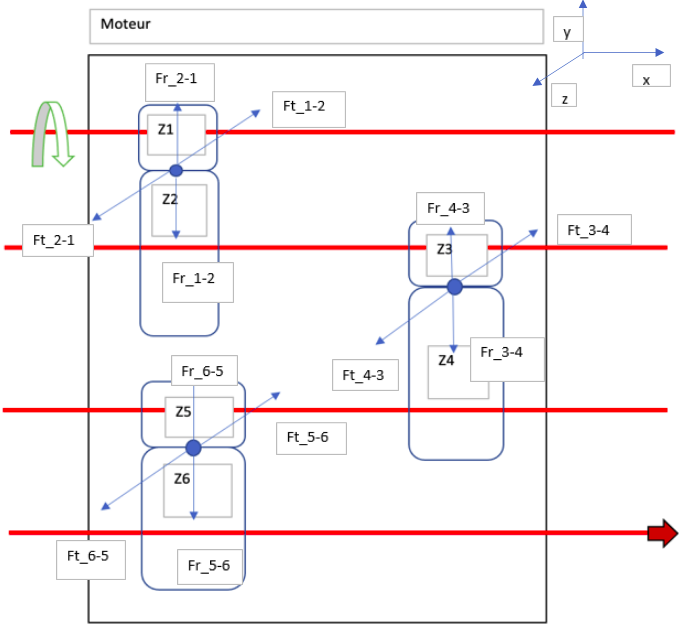
Image 3 : Schéma du réducteur à trois étages
(représentant les quatre arbres ou axes, les trois
engrenages et les forces s’appliquant sur ces derniers).
Pour continuer, nous devions trouver le nombre de dents adéquat pour chacune des roues et chacun des pignons. Pour faire cela, nous avons utilisé le solveur du logiciel Excel.
Nous avions plusieurs conditions à imposer, comme un nombre minimal de dents, le taux de réduction devait être compris dans un intervalle de 20% autour de sa valeur calculée, la masse de l’ensemble devait être la plus faible possible, etc.
Grâce aux calculs du solveur, nous avons obtenu les nombres optimaux de dents.
Ceci nous a ensuite permis de calculer le module de chacun des trois engrenages, un paramètre relatif à la périodicité et à la taille de ces mêmes dents.
Après avoir obtenu les modules, nous les avons normalisés (rapprochés d’une valeur entière normée et plausible).
Ensuite, comme nous avions toutes les caractéristiques nécessaires des engrenages, nous avons calculé les forces radiales et tangentielles (représentées sur l’Image 3) s’appliquant sur eux.
En effet, lorsque un pignon tourne, il va appliquer une certaine force sur la roue située au-dessous de lui, provoquant ainsi le phénomène de rotation. Ce sont donc ces forces que nous avons cherché à calculer.
C’est en utilisant à nouveau le Principe Fondamental de la Statique et des torseurs, que nous avons trouvé les valeurs des forces. Après avoir additionné ces dernières en respectant leur orientation dans notre repère cartésien, nous avons finalement obtenu trois forces générales, appliquées sur
chaque engrenage.
En nous rappelant qu’un de nos objectifs était de diminuer au maximum la masse du réducteur, nous avons rapprochés les engrenages entre eux. C’est donc en considérant la largeur des pignons, des roues et des roulements placés aux extrémités des arbres (roulements assurant la rotation des quatre arbres) que nous avons pu établir les distances minimales (appelées entretoises) entre tous les éléments intérieurs du réducteur.
Avec ces distances minimales, nous avons encore une fois utilisé le Principe Fondamental de la Statique et nos formules de Propriétés et Résistance des Matériaux, sur chacun des quatre arbres.
Cela nous a permis de connaître les valeurs des contraintes (principalement la flexion) subies par ces derniers. Enfin, c’est avec ces dernières valeurs calculées que nous avons déterminé le diamètre minimal à adopter pour chaque arbre.
Tout ceci achevé, il nous restait à choisir les différents composants nécessaires au bon fonctionnement du réducteur. C’est après avoir calculé les différentes vitesses de rotation des arbres, les couples transmis (le mouvement de rotation) et les forces appliquées sur chaque arbre, que nous avons choisi les roulements (différents de ceux utilisés plus haut, qui avaient été arbitrairement choisis, sans connaître les diamètres des arbres).
Nous avons ensuite sélectionné les épaulements (pièce mécanique servant à bloquer les roulements, pour leur empêcher tout mouvement) à partir des caractéristiques des roulements choisis.
Comme nous avons changé le type de roulement (rappelez-vous que nous avons arbitrairement considéré des roulements, au moment de calculer les entretoises entre tous les éléments intérieurs au réducteur !), nous avons dû recalculer ces distances minimales avec nos nouveaux roulements et nos épaulements.
Suite à cela, nous avons choisi d’après les diamètres minimaux des arbres, huit anneaux élastiques afin de maintenir les roulements et les arbres en place.
Pour terminer, nous avons choisi des clavettes (pièce mécanique se plaçant entre un pignon ou une roue et l’arbre en rotation auquel il/elle appartient) grâce à des formules spécifiques, décrivant la longueur minimale de ces dernières. Il s’agissait ici de calculer les contraintes que subiront ces six clavettes, pour chaque engrenage, afin de déterminer la longueur minimale à adopter, pour obtenir une résistance optimale.
3) Conclusion de notre projet de conception
Ce projet de conception, que nous avons réalisé durant notre quatrième semestre d’études, nous aura permis de réellement nous familiariser sur des sujets, au premier abord, compliqués.
Comme précisé au début de cet article, nous n’étions pas vraiment à l’aise avec les notions vues dans notre module de Propriétés et Résistance des Matériaux, ce que nous souhaitions donc changer.
Concevoir ce carrousel simplifié a été un véritable défi, où nous avons pu nous surpasser, tant sur le plan théorique que sur le plan humain.
Travailler avec d’autres personnes sur un projet commun est quelque chose de très enrichissant.
Cela nous permet d’exprimer notre point de vue, mais surtout de comprendre et de s’ouvrir à d’autres visions différentes de la notre : ce qui reste l’une des qualités les plus importantes d’un futur ingénieur.
______________________________________________________________________
Résistance des matériaux : discipline permettant d’étudier le comportement de différents matériaux au niveau local (sur un petit volume d’une pièce), de façon à étendre ce même comportement au niveau global (c’est-à-dire, à l’entière pièce considérée) et de calculer de façon détaillée les contraintes et les déformations subies par un matériau sous l’effet d’une sollicitation particulière (par exemple, le poids).
Analyse des systèmes mécaniques : discipline permettant l’étude de différents systèmes mécaniques comme un moteur de voiture, par exemple) à partir d’un schéma fonctionnel. Cette discipline est aussi utile pour déterminer les liaisons reliant des pièces entre elles et sert à choisir les composants qui permettent d’obtenir une telle liaison (un roulement à billes autorise une liaison pivot). Enfin, cette discipline intervient dans les transmissions de puissance, à travers des engrenages notamment.
Contrainte de cisaillement : contrainte mécanique appliquée de manière parallèle ou tangentielle à la face d’un matériau considéré.
Contrainte de traction : contrainte mécanique appliquée de manière perpendiculaire à deux faces opposées d’un matériau considéré, de façon à l’étirer pour mesurer le moment de rupture.
Crédits de l’Image 1 : Swing ride in Santa Cruz, the county seat and largest city of Santa Cruz County, California, photographie par Carol Highsmith, le 9 juin 2012, collection de la Bibliothèque du Congrès des États-Unis d’Amérique, œuvre placée dans le domaine public.
Les Image 2 et Image 3 ont été respectivement créées par Virgile Siegler et Alexi Schmid, dans le cadre de ce projet de conception.