Bonjour, nous nous présentons : Anthony De Sa et Antoine Quémerais. Nous sommes deux étudiants en deuxième année de classe préparatoire à Polytech Angers. Cette année, nous avons eu l’occasion de choisir un projet de fin d’études. Étant tous les deux passionnés de mécanique, de sport automobile et d’innovation en général, nous nous sommes dirigés vers celui d’une caisse à savon autonome. L’objectif de ce projet était de créer une caisse à savon sans aucune base existante et de la rendre autonome pour qu’elle puisse participer à une course sans pilote.
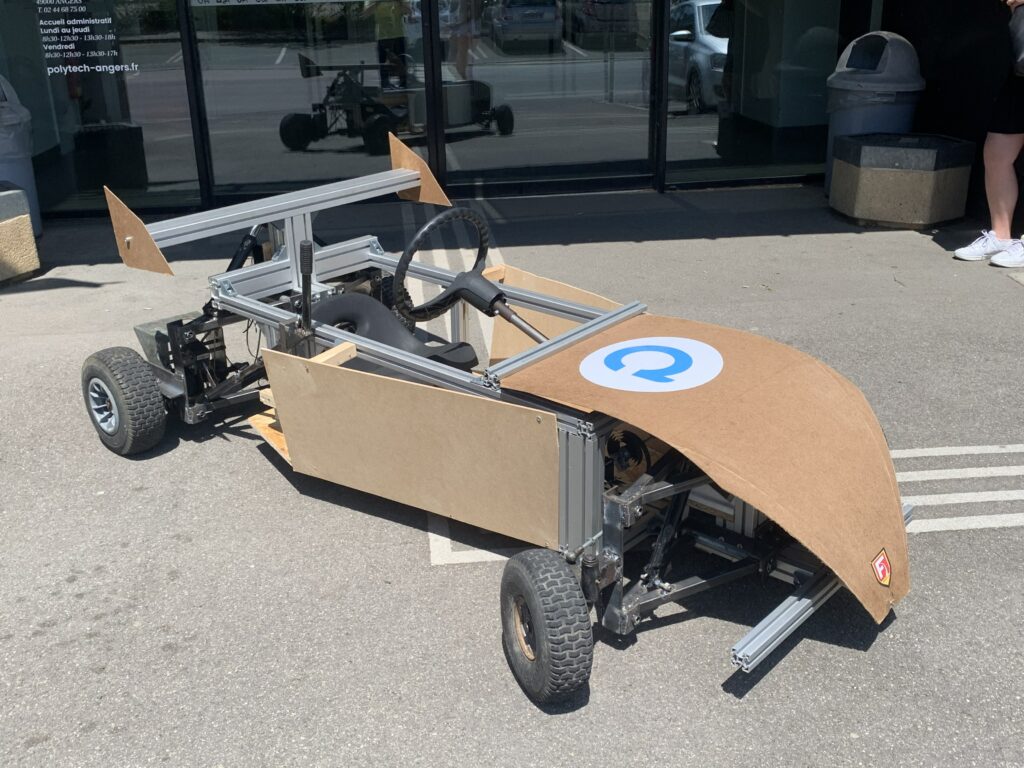
Monsieur Lagrange est le professeur qui nous a encadrés tout au long de notre projet et qui nous a apporté des conseils. Les exigences qu’il attendait sur ce projet étaient :
- avoir une caisse à savon compacte et assez légère pour la déplacer et la stocker
- avoir la possibilité qu’un humain puisse la conduire
- avoir un système automatisé afin que la voiture puisse se diriger et freiner par elle-même
Pour se repérer dans l’espace, Anthony a fait le choix d’un capteur laser aussi appelé capteur lidar. Un capteur lidar permet de savoir à quelle distance se trouve un objet par rapport à ce dernier. De plus, celui-ci est placé sur un servomoteur permettant une vision à 360 degrés. Sur les conseils de monsieur Lagrange, nous avons choisi le capteur lidar le plus adapté à notre utilisation. Les données du capteur lidar devaient être récupérées par un Raspberry (type de micro-ordinateur), qui devait les analyser, puis aurait calculé la meilleure trajectoire à prendre. Une fois la meilleure trajectoire calculée, le Raspberry devait donner les instructions à l’Arduino pour qu’il puisse réorienter la direction ou freiner. Cependant, cette étape a été fortement ralentie, car la livraison du capteur lidar prit plus d’un mois. Il nous était donc impossible d’avancer sur la partie électronique.
Aimant les défis, nous nous sommes rajouté une grosse difficulté : celle d’avoir des suspensions indépendantes sur chaque roue. Nous avons trouvé cette difficulté challengeant et plus amusante dans la réalisation de la caisse à savon.
À partir du moment où nous avions toutes les exigences attendues, nous étions prêts à pouvoir commencer la modélisation.
Nous nous sommes d’abord réunis autour d’une feuille et d’un ordinateur pour concevoir le châssis et la structure globale de la caisse à savon. Nous avons longuement échangé sur les différentes possibilités que l’on pouvait mettre en œuvre, mais aussi adapté notre conception en fonction du matériel mis à notre disposition. Après de longues heures de discussion, nous nous étions mis d’accord sur une idée de conception et une allure globale.
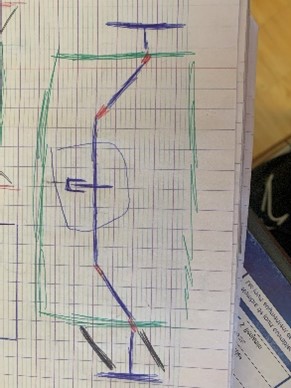

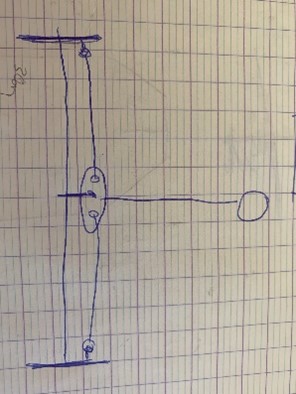
Nous pouvions maintenant passer à la modélisation 3D de cette caisse à savon sur le logiciel SolidWorks. Cette étape était indispensable et essentielle pour la suite de notre projet. La modélisation 3D permettait de voir si tous les mécanismes mis en œuvre fonctionnaient et étaient réalisables. Mais également de constater la taille de la caisse à savon et ses limites de résistance mécanique. Après de nombreux essais, nous avions notre version finale. Cette version a été validée par notre tuteur. Nous étions prêts à passer à la construction du châssis.
La mécanique
Pour la construction du châssis, nous avons récupéré des profilés en aluminium que nous avons assemblés avec des équerres en aluminium. Cela nous permettait de profiter d’une grande légèreté tout en gardant une bonne rigidité et une bonne résistance mécanique.
Pour la direction, le freinage et les suspensions, aucun matériel n’était mis à notre disposition. Nous devions donc nous débrouiller pour les trouver sur des sites marchands partenaires de l’école. Cette étape d’apparence simple était très fastidieuse. Nous n’avions accès qu’à une certaine gamme de produits, ce qui était très handicapant et nous limitait dans la conception. Après de nombreux compromis, nous avons passé notre commande pour la construction du système de suspensions. Nous avions décidé de partir sur un système de suspension en triangulation avec des paliers lisses en bronze comme roulement, des tubes en acier comme structure, et des suspensions de fourches de vélo découpées comme amortisseurs, récupérées dans un vieux local à vélos.
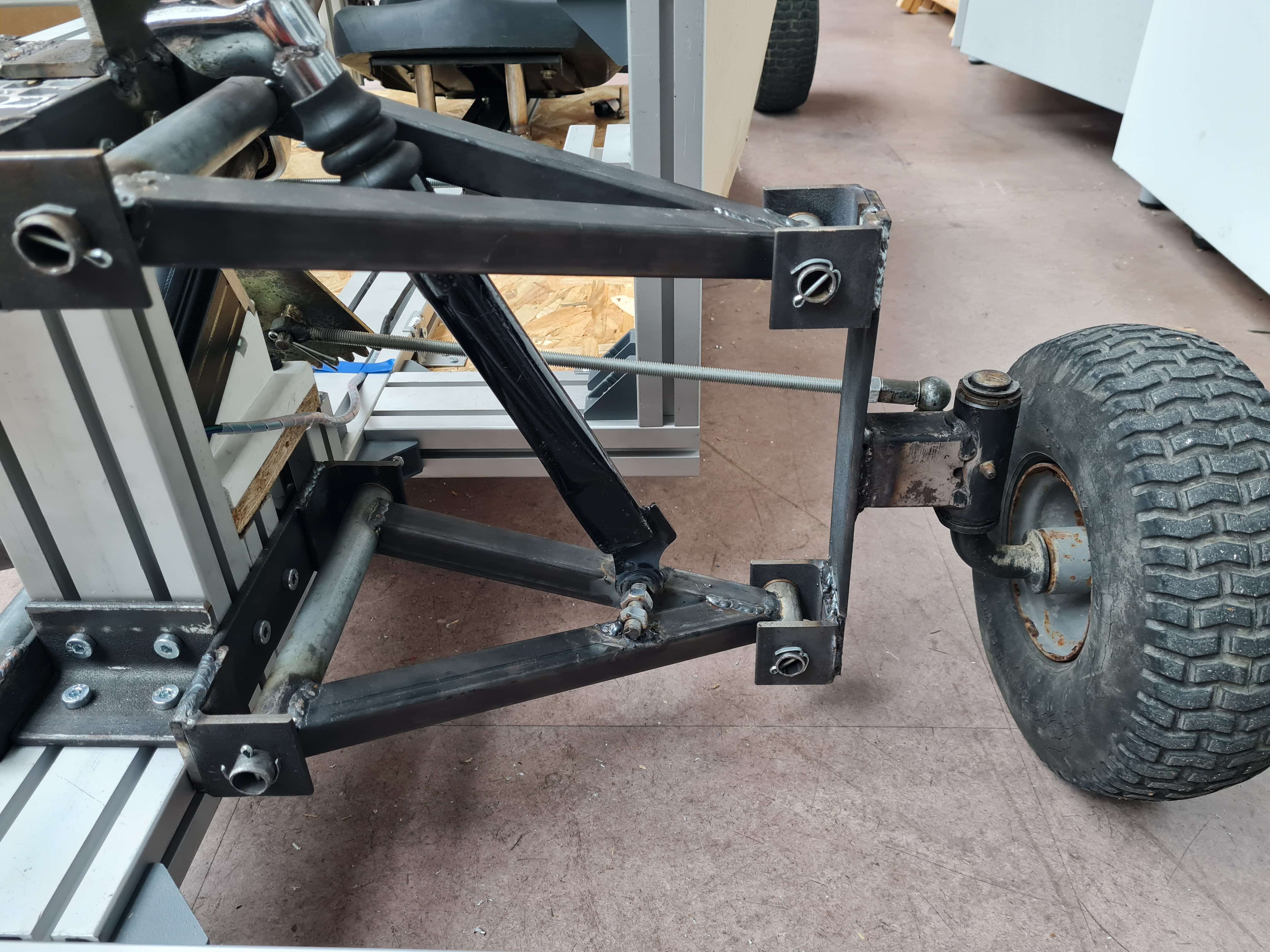
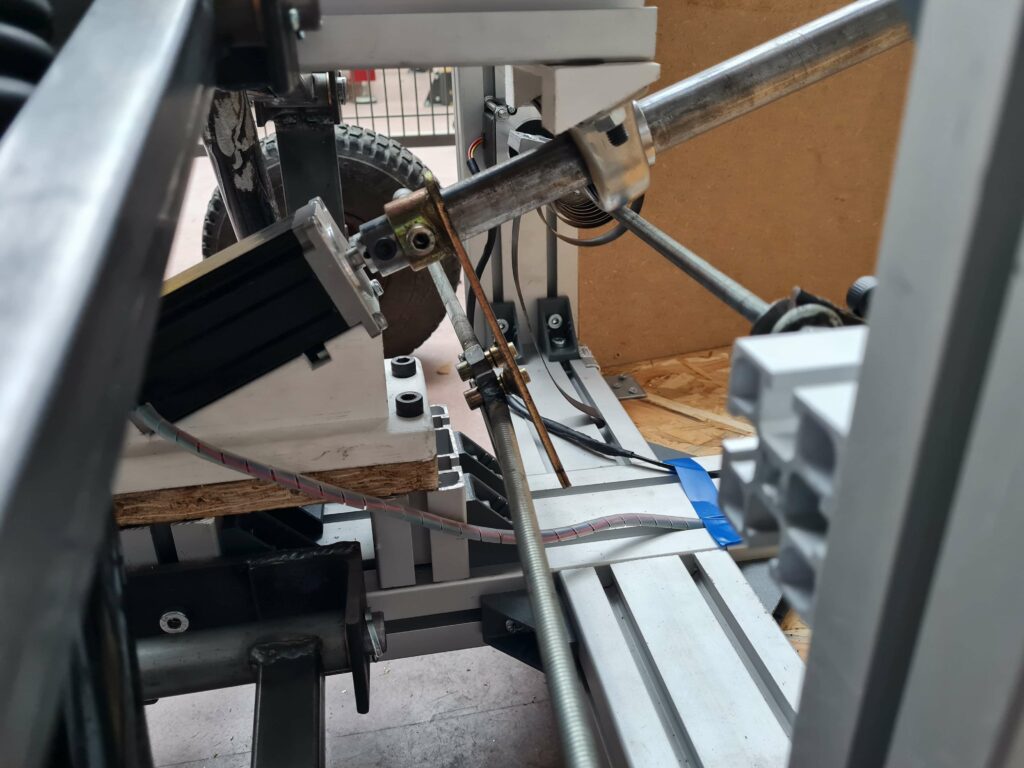

Malheureusement pour nous, les délais de livraison étaient assez importants. Nous devions aller chercher certaines pièces sur place dans les magasins et d’autres arrivaient par livraison. Nous étions alors fortement freinés dans notre avancement à raison de plusieurs semaines (3-4 semaines). Nous avions compris que le temps nous était compté et qu’il fallait être très efficace si nous voulions finir dans le temps impartis. Pour optimiser notre temps, nous nous étions alors réparti le travail selon nos points forts respectifs : Anthony devait se charger de la partie électronique et Antoine de la partie mécanique.
L’électronique
Anthony a décidé de contrôler la direction et le freinage à partir de moteurs pas à pas récupérés sur une vieille CNC (machine de découpe numérique). Les moteurs pas à pas ont la particularité de pouvoir se contrôler avec une grande précision et ainsi pouvoir choisir précisément l’angle de rotation de la direction et du freinage. C’était la solution la plus adaptée à notre projet. Chaque moteur est piloté à partir de drivers récupérés également sur la CNC. L’ensemble des drivers est contrôlé par un Arduino qui nous permet de transmettre toutes les instructions aux moteurs. L’Arduino est la solution la plus adaptée, car c’est un microcontrôleur très simple à programmer et à connecter.
Nous pouvions maintenant passer à la modélisation 3D de cette caisse à savon sur le logiciel SolidWorks. Cette étape était indispensable et essentielle pour la suite de notre projet. La modélisation 3D permettait de voir si tous les mécanismes mis en œuvre fonctionnaient et étaient réalisables. Mais également de constater la taille de la caisse à savon et ses limites de résistance mécanique. Après de nombreux essais, nous avions notre version finale. Cette version a été validée par notre tuteur. Nous étions prêts à passer à la construction du châssis.
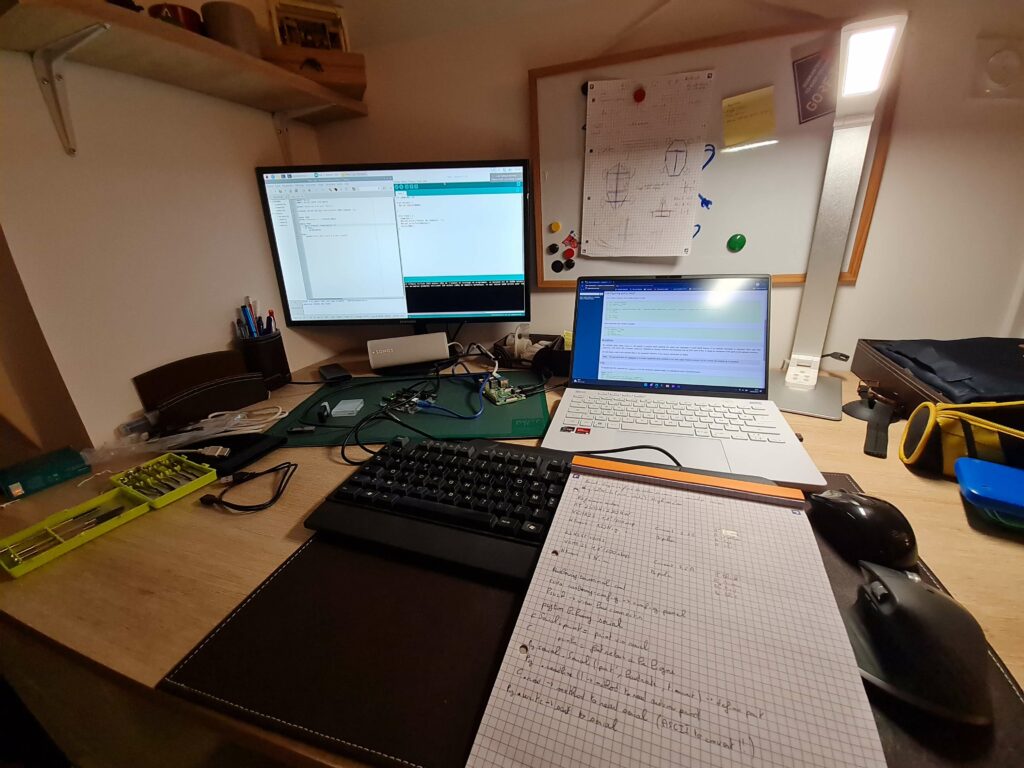
L’assemblage
Dans le même temps, toutes les pièces du système de suspension étaient arrivées. Pour assembler le tout, il était indispensable de faire de nombreuses soudures, cependant l’établissement n’était pas équipé de ce matériel. Antoine a alors décidé de ramener entièrement la caisse à savon chez lui, dans le but de se faire aider par son père qui avait des connaissances en soudure et possédait l’équipement nécessaire chez lui. Antoine et son Père ont passé les vacances d’avril à assembler, à souder et à construire la caisse à savon. Il serait fastidieux de rentrer dans les détails de chaque soudure et mécanisme créés. Cependant, vous pouvez voir ci-dessous les photos de l’ensemble du travail effectué. Cette partie de la construction a mobilisé beaucoup de temps de travail et nécessité beaucoup de débrouille, car l’approche théorique et la modélisation 3D ne fonctionnaient pas exactement de la même façon dans la réalité. Cela a demandé beaucoup d’adaptation et de patience.
Il a fallu un peu d’ingéniosité pour adapter la partie existante du tracteur tondeuse sur la caisse à savon.
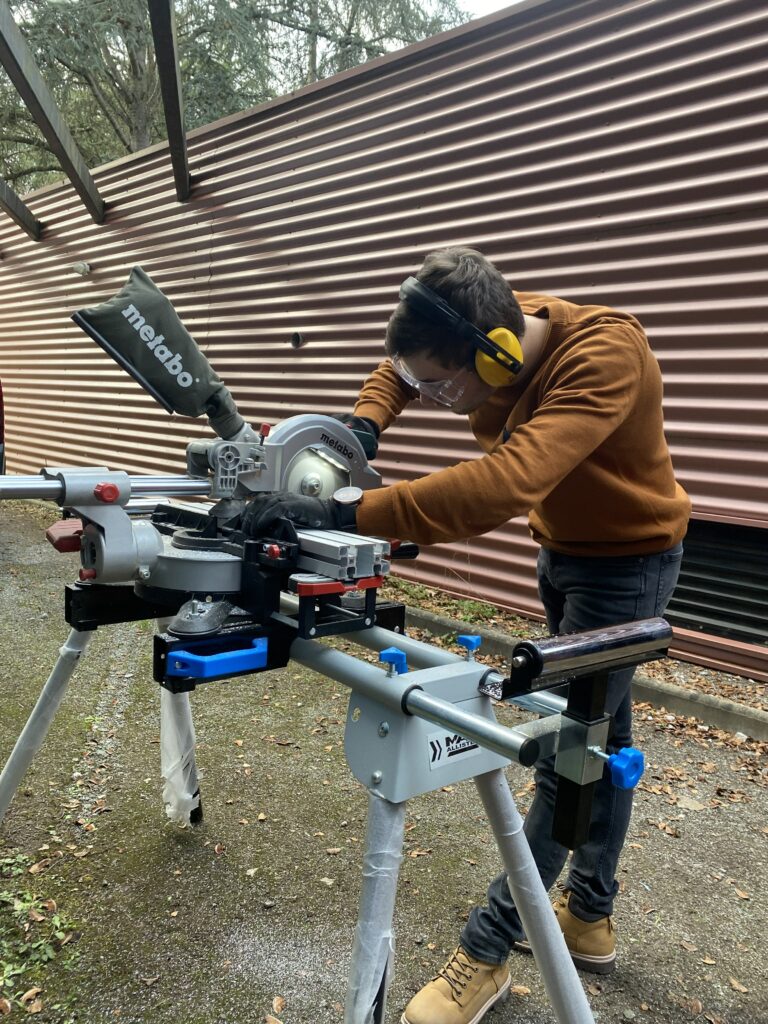
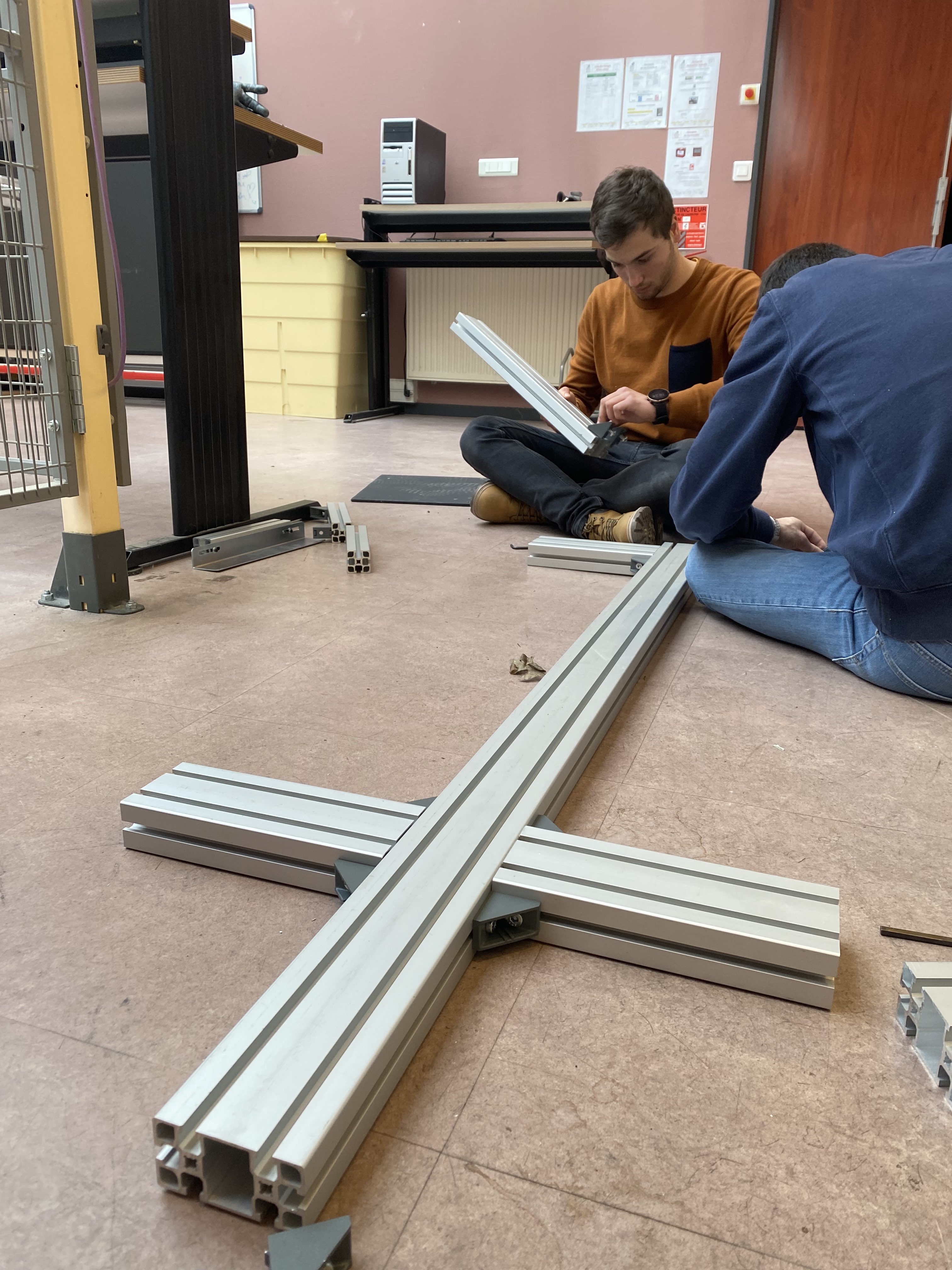
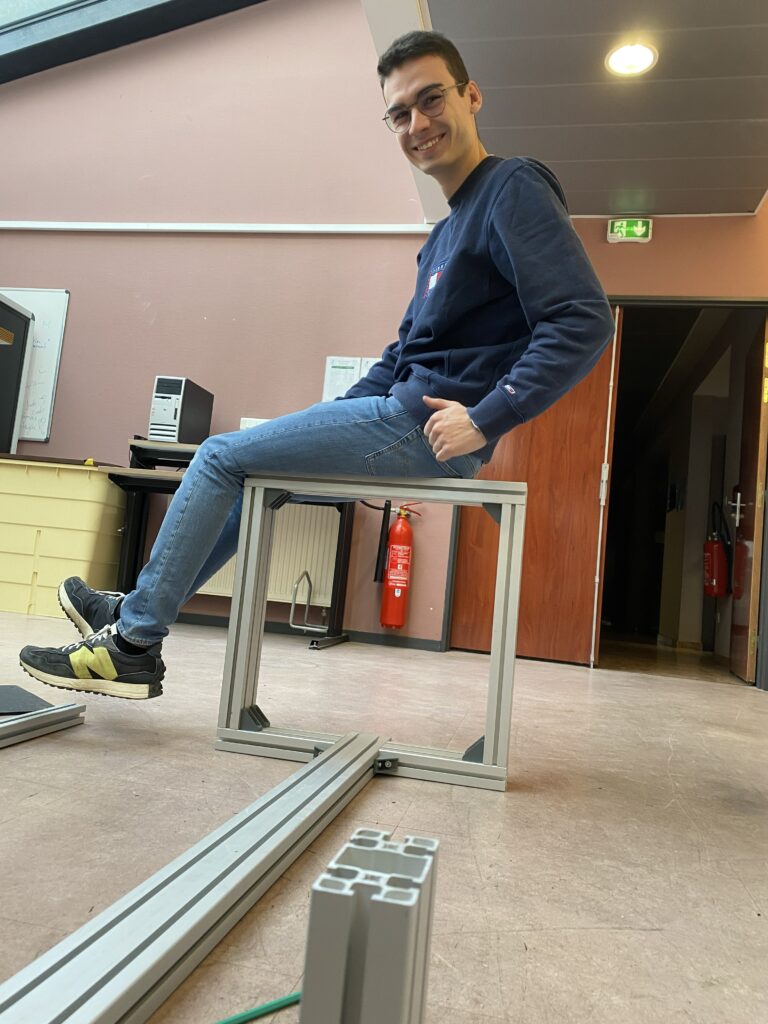
Une fois cette partie mécanique et électronique faite, il s’était écoulé environ 1 mois. Il était temps de fusionner les deux parties. Antoine a ramené la caisse à savon à Angers et Anthony a adapté l’électronique et les moteurs dessus. Plusieurs problèmes ont été rencontrés :
- Problème d’accouplement entre le moteur et le volant
- Les suspensions de vélo récupérées étaient un peu trop faibles pour la caisse à savon
- Le frein était très dur à mettre en œuvre. On ne pouvait pas tirer le câble jusqu’à la pédale de frein, trop de frottement. Il fallait également jumeler les 2 roues avec un système de cardan pour que les 2 roues freinent
Il fallait donc que nous trouvions des solutions à ces problèmes majeurs. Le problème d’accouplement a été rapidement réglé grâce à une pièce achetée, qui permettait de relier le moteur et l’axe du volant. Pour les suspensions, malheureusement nous ne pouvions pas les changer pour en avoir de plus performantes, du fait du manque de temps et de problème de temps de livraison. Pour le système de freinage, nous avons opté pour un système de levier plus simple et plus rapide à mettre en place. Pour jumeler les 2 roues, nous avons acheté des joints de cardans, cependant les délais de livraison restaient importants et il nous restait peu de temps pour finir le projet.
Lors de la livraison du fameux capteur lidar, nous avons été confrontés à un nouveau problème. L’utilisation du capteur lidar était très complexe, voire incompréhensible pour notre niveau de connaissance. Nous avons dû faire appel à notre tuteur, mais également à monsieur Guyonneau, enseignant spécialisé en informatique, pour parvenir à faire fonctionner ce capteur et le comprendre. Malheureusement, la tâche était ardue et longue pour eux également. Face à une telle complexité pour programmer ce capteur, qui dépassait totalement nos compétences, et le temps restant, monsieur Lagrange a trouvé plus raisonnable de supprimer cette partie du projet.
Nous nous sommes alors plus concentrés sur la partie mécanique de la voiture. Pour lui rajouter un aspect esthétique, nous avons commencé à ajouter un plancher et de la carrosserie, mais également des autocollants et un logo.
Malheureusement, le temps qui nous était imparti a été rapidement écoulé. Nous sommes à la fin du projet. Voici l’état du projet final :
- Le châssis est fini, rigide et fiable
- Les 4 suspensions sont opérationnelles
- La direction et les frein fonctionnent
- Le plancher est fixé
- Tous les moteurs et l’électronique ont été intégrés dans la caisse à savon
Malgré tout le travail que nous avons fait, nous n’avons pas pu aller au bout de tous nos objectifs. Les points qui nous restaient à faire étaient :
- Intégrer le capteur lidar,
- Jumeler les 2 roues avec les cardans qui sont arrivés la veille de la fin du projet
- Faire toute la programmation pour rendre la voiture autonome
Malgré le fait que nous n’ayons pas eu le temps d’aboutir pleinement le projet, nous sommes très fiers du travail accompli. Il s’agissait d’un projet ambitieux que nous avons aimé faire et dans lequel nous nous sommes épanouis. Nous avons donné notre maximum pour qu’il voie le jour.
Nous avons pu tester la caisse à savon à plusieurs reprises, et également donner ce privilège à d’autres étudiants. L’expérience de conduite est très satisfaisante et le regard admiratif des professeurs et des élèves à la vue de la caisse à savon nous réjouit énormément. Nous sommes heureux d’avoir pu construire un véhicule qui fait parler de lui et qui partage des émotions. Au-delà d’être une simple caisse à savon, c’est un projet qui nous aura appris beaucoup de choses, et ce dans de nombreux domaines.
Nous espérons que le récit de cette aventure vous donnera également l’envie d’entreprendre des projets encore plus fous et ambitieux que le nôtre. Nous espérons que les futurs étudiants pourront reprendre notre travail et arriver à la concrétisation de notre projet.
Nous tenons à remercier toutes les personnes qui ont permis la réalisation de ce projet. Nous pensons en premier à Boris pour son aide au FabLab, au père d’Antoine pour son investissement dans le projet, à Motoculture Dol Service pour sa contribution, à Monsieur Guyonneau pour son aide en informatique et à Monsieur Lagrange pour son implication dans le projet.
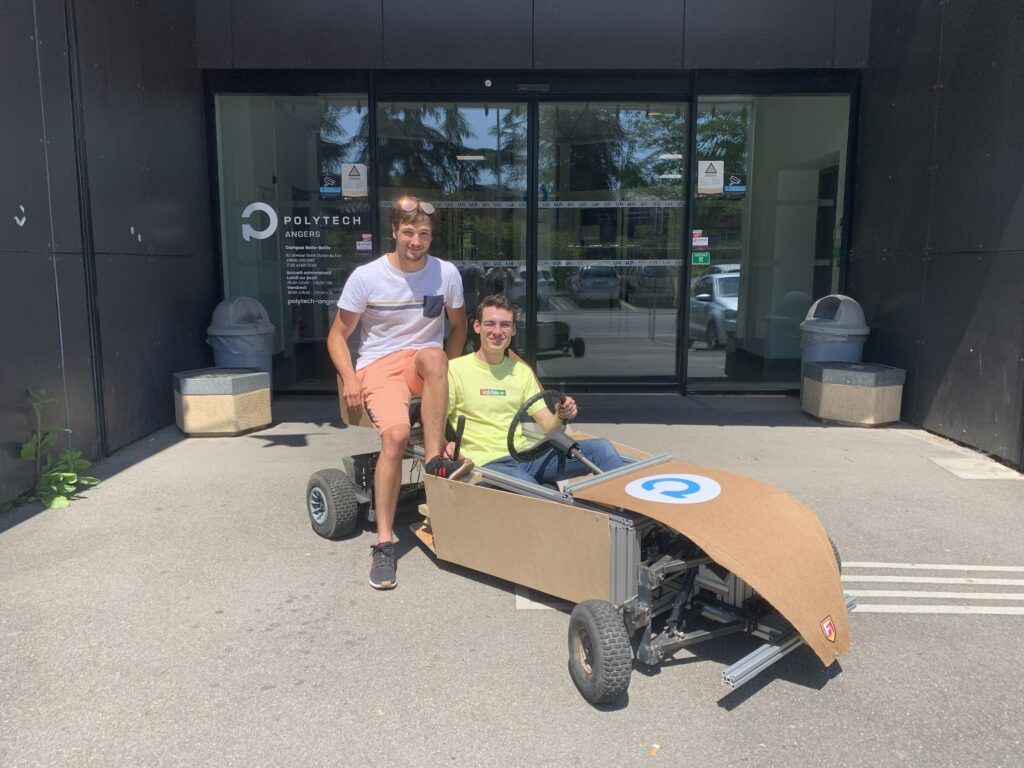
Merci à tous pour votre lecture!