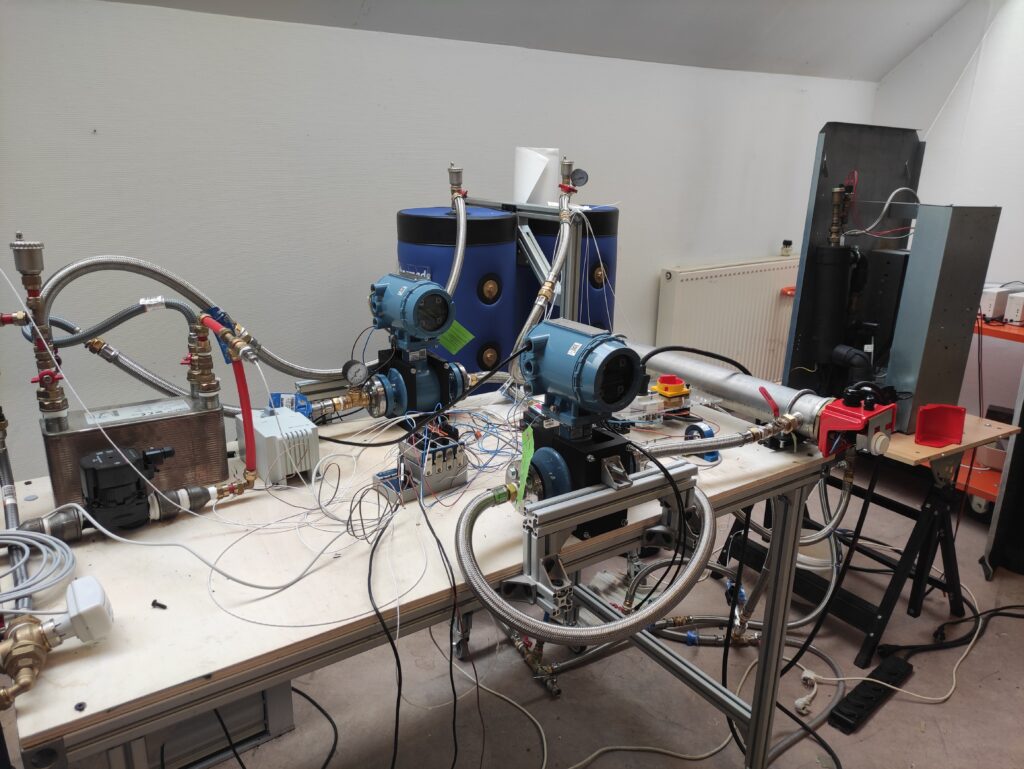
Bonjour à toutes et à tous !
Nous sommes Maël, Hugo et Nathan, trois étudiants en deuxième année du cycle préparatoire à l’école Polytechnique de l’Université d’Angers.
Avant toutes choses nous tenons à remercier toutes les personnes qui ont contribué à la réalisation de ce projet.
Nous voudrions dans un premier temps remercier, Rima AL ARIDI et Bassel CHOKR, les deux doctorants que nous avons assisté pendant ce projet et qui nous ont appris de très nombreuses notions avec une grande pédagogie malgré la barrière de la langue. Nous les remercions aussi pour leurs conseils, leur bienveillance et leur patience.
Ensuite nous voudrions remercier Hassan BOULJROUFI, assistant ingénieur électronique, pour son expertise sur la partie électrique et électronique du projet ainsi que pour ses nombreux conseils vis-à-vis de l’apprentissage de LabVIEW, de la réalisation de notre rapport et de notre rôle en tant qu’étudiant de deuxième années.
Enfin nous remercions Thierry LEMENAND, enseignant chercheur et responsable du projet, pour nous avoir donné la possibilité de travailler avec toutes ces personnes au sein de ce projet qui nous dépasse en tant qu’étudiant de deuxième années.
Contexte :
Lorsque l’on parle des principaux secteurs émetteurs de gaz à effet de serre, on évoque souvent le secteur du transport ou celui de l’industrie. Pourtant il existe d’autres secteurs occupant une part importante des émissions de gaz à effet de serre, comme le secteur du bâtiment. En effet, d’après les chiffres du Ministère de la transition écologique, ce secteur représente 23% des émissions de gaz à effet de serre en France ainsi que 43% des consommations énergétiques annuelles françaises. Afin de réduire cet impact, il est donc impératif de rénover les bâtiments mal isolés ou de favoriser l’installation de systèmes énergétiques plus performants et plus sobres, comme la pompe à chaleur.
Cependant, la pompe à chaleur actuelle n’est pas un dispositif parfait en termes d’émissions…
Pourquoi la pompe à chaleur classique présente une imperfection majeure ?
En effet, afin de fonctionner correctement, la pompe à chaleur thermodynamique doit utiliser des fluides frigorigènes car ces fluides permettent de transférer les calories extérieures à l’intérieur de l’habitation en utilisant le principe de compression / décompression. Ces fluides ayant un potentiel de réchauffement très élevé, en comparaison le CO2 a un potentiel de 1, car c’est l’unité de référence créée par le GIEC, tandis que le fluide R32, le plus utilisé pour les pompes à chaleur, en a un de 675, selon l’AFCE.
Heureusement des solutions pour remédier à ce problème existent !
Le projet ARKTEA
C’est donc pour faire disparaître les émissions dues aux fluides frigorigènes que le projet ARKTEA est né. Ce projet est le fruit d’une alliance de 4 entreprises françaises :
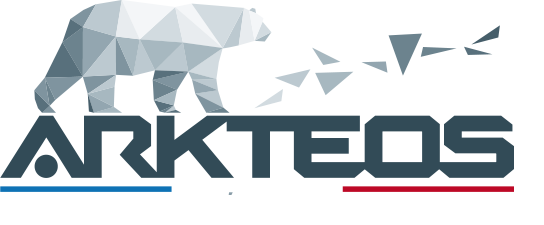
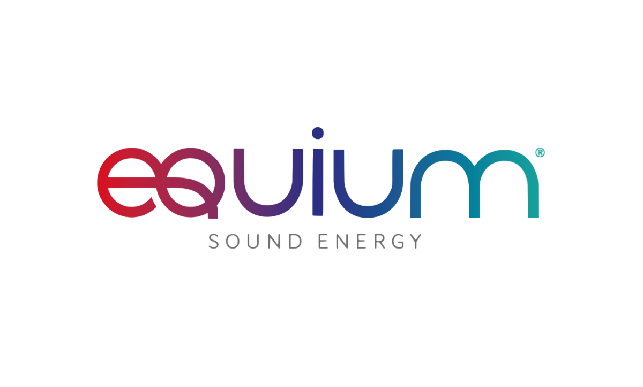

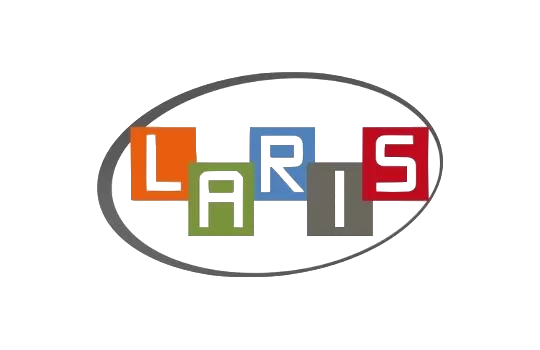
Le son au service l’environnement
Afin de remplacer les fluides frigorigènes et leur rôle au sein de la pompe, l’entreprise Equium a donc décidé de développer une pompe à chaleur utilisant le principe de la thermoacoustique. En effet, tout son est un mouvement d’ondes et comme on peut le voir sur l’animation suivante, ces ondes effectuent un mouvement de compression et de décompression ce qui permet de produire à la fois du chaud et du froid, tout comme les fluides frigorigènes :
Bien évidemment, ce principe est naturel et n’émet quasiment pas de gaz à effet de serre.
“On pourrait se libérer de la menace climatique qui pèse sur nos têtes en changeant les règles du jeu, maintenant, en favorisant les écotechnologies comme la thermoacoustique.”
cédric françois, fondateur d’equium, TED x Rennes
Pourquoi trois étudiants de Polytech Angers ont un rôle à jouer dans ce projet ?
Comme dit précédemment, le laboratoire Laris participe à ce projet avec la création d’un banc d’essai pour la pompe à chaleur.
Ce banc constitue le projet de thèse de deux doctorants Libanais, Bassel et Rima. En tant qu’étudiant de deuxième année, nous avions plusieurs objectifs sur ce projet dont deux principaux. La première partie de notre travail consistait à réaliser l’acquisition de plusieurs températures et plusieurs voltages. Ces données sont issues de sondes de températures appelées PT100 et de débitmètres. Pour la deuxième partie principale, il nous était demandé de contrôler une résistance chauffante et notamment de la maintenir à une certaine température. Enfin, pendant toute la durée du projet nous avons été amenés à réaliser différentes tâches manuelles en plomberie et en électricité.
LabVIEW : un logiciel multitâches et très puissant
Afin de réaliser nos deux tâches principales, nous avons utilisé un logiciel de National Instruments nommé LabVIEW. Contrairement à d’autres langages de programmation comme le Python ou le langage C, la programmation sur LabVIEW s’effectue de manière beaucoup plus visuelle avec des blocs reliés entre eux.
On peut constater cela avec l’exemple suivant, illustrant la relation des gaz parfaits :
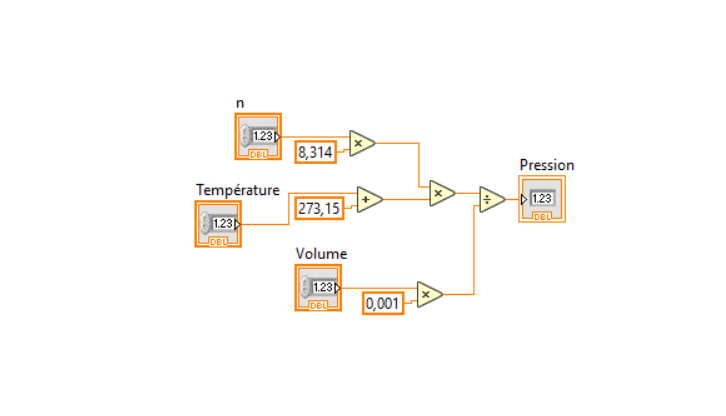
Un programme LabVIEW est constitué de deux parties avec le block diagram comme ci-dessus et le front panel comme ci-dessous.
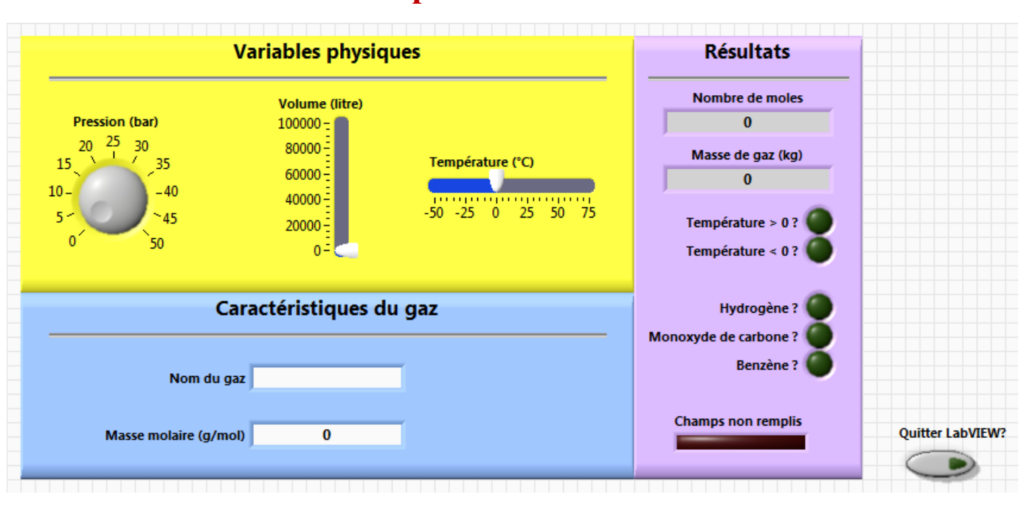
Acquérir des données et les classer avec LabVIEW
Afin de récupérer les différentes données de notre banc d’essai, nous avons donc construit un programme LabVIEW.
Pour commencer, nous avons réalisé une horloge permettant de définir la durée d’acquisition.
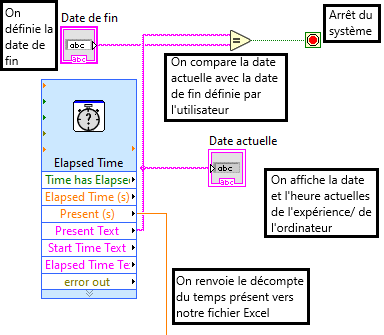
Ensuite, nous devions récupérer les données. Pour cela nous avons utilisé, sur le banc, des cartes d’acquisition liées aux différents capteurs de données et le module DAQ assisant sur LabVIEW.
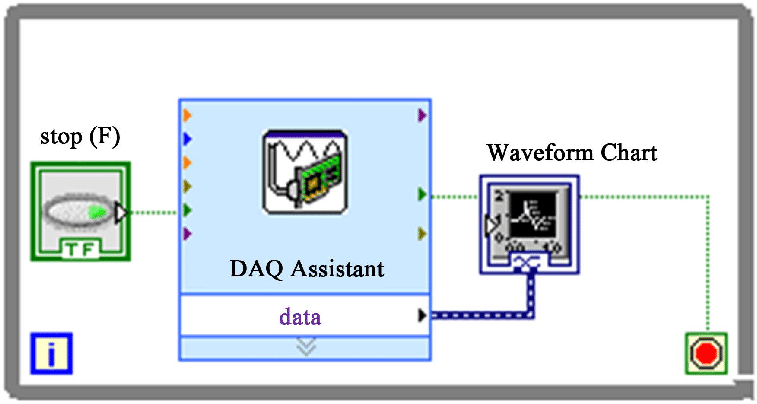
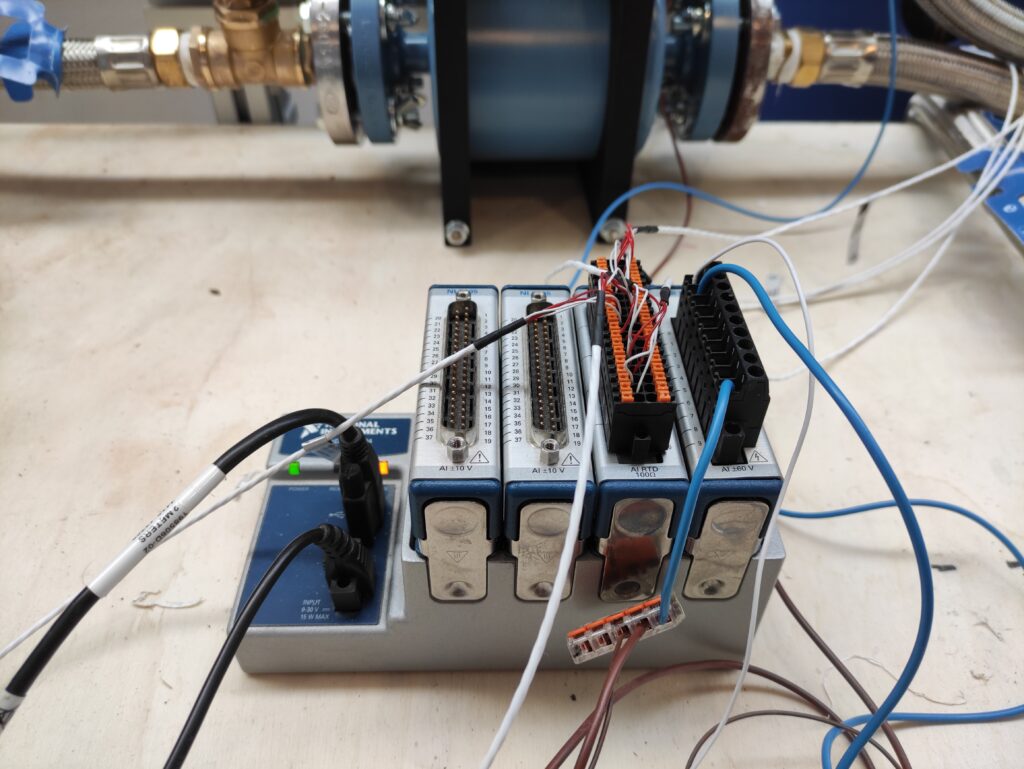
Cela nous a permis de transférer les données du banc d’essai vers l’ordinateur.
Après cela, nous devions convertir ces données en tableau pour les classer dans un fichier Excel. Pour cela, nous avons donc utilisé ces deux premières parties du programme général.
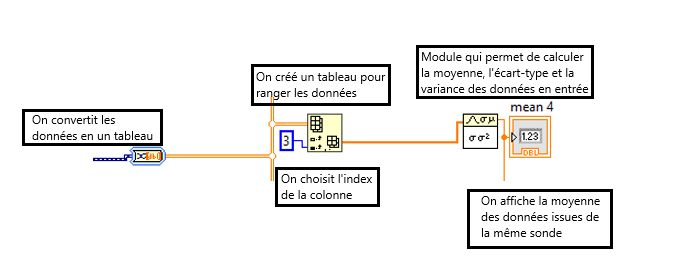
Ici on cherche à récupérer la moyenne des valeurs de chaque capteur pour avoir une seule valeur toutes les x secondes.
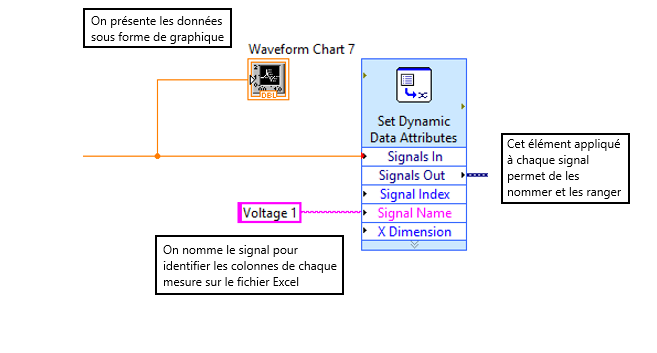
Cette partie du programme nous permet ici de créer une colonne de tableau pour chaque données avec un nom associé.
Les deux programmes ci-dessus sont donc répétés autant de fois que nous avons de capteurs, soit huit.
Enfin, nous avons relié ces sept parties du programme à un module nommé “Write to measurement file” pour créer le fichier Excel avec les données.
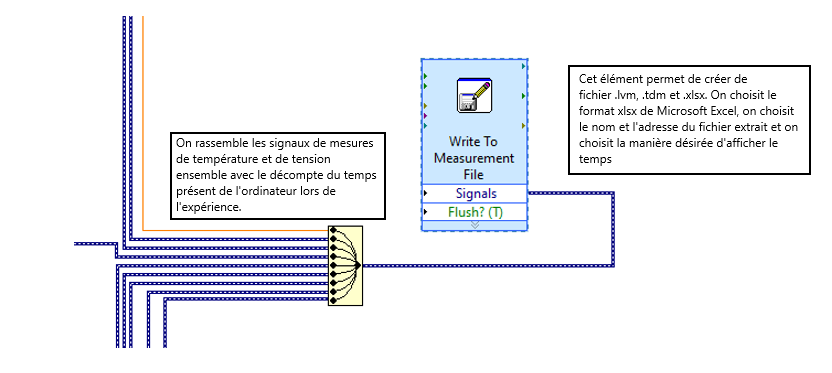
Contrôler une résistance chauffante avec LabVIEW
Pour cette partie, il nous était demandé de maintenir à une certaine température une résistance chauffante présente sur la banc d’essai. Cette résistance a pour but de chauffer l’eau en provenance de la pompe à chaleur.
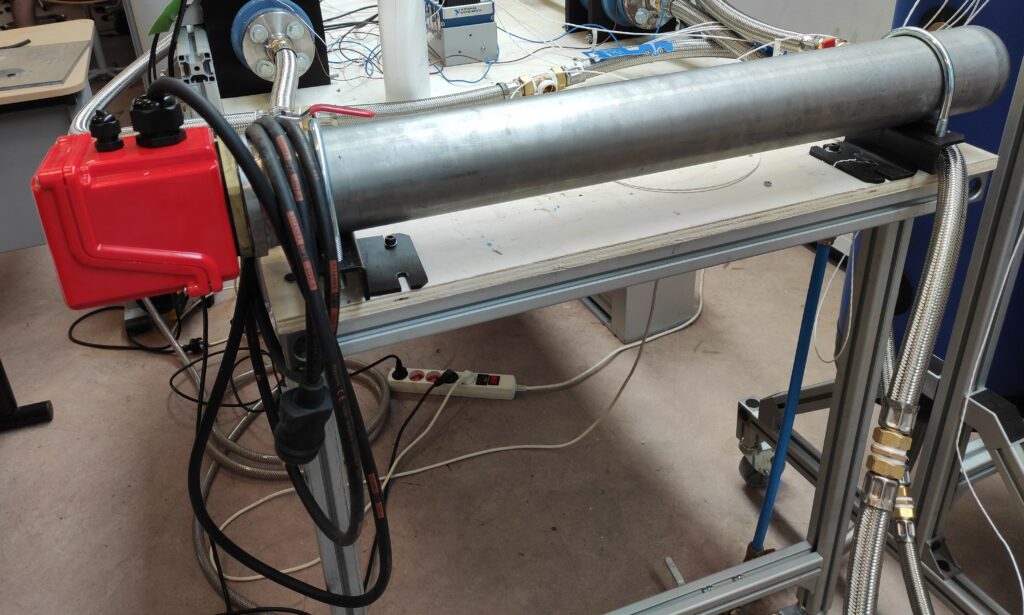
Pour contrôler cette température avec LabVIEW, nous avons utilisé le principe de la régulation. Pour illustrer ce qu’est la régulation, nous pouvons prendre l’exemple d’un régulateur de voiture. En effet, lorsque l’on souhaite que notre voiture roule à 110 km/h, l’ordinateur de bord va calculer la puissance que le moteur va devoir délivrer afin de maintenir la vitesse désirée selon la forme de la route par exemple.
Pour en revenir à notre projet, nous avons conçu un programme LabVIEW utilisant le module de régulation PID ( Proportionnel Intégrale Dérivée) présent sur la version améliorée du logiciel.
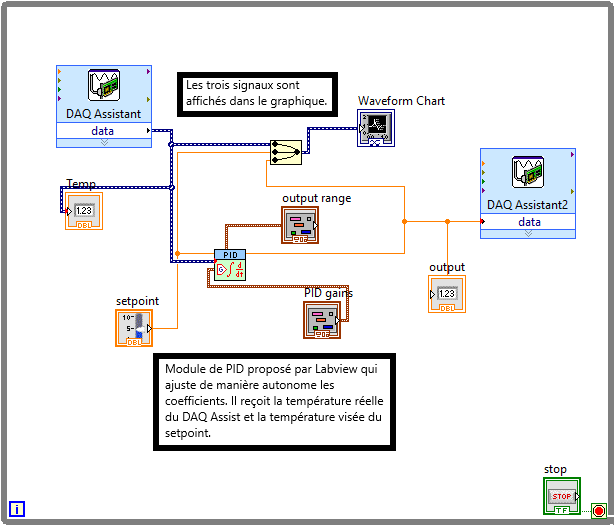
Grâce à ce programme, nous pouvons chauffer notre résistance à la température souhaitée et en optimisant les paramètres de PID, avoir une régulation des plus optimisées.
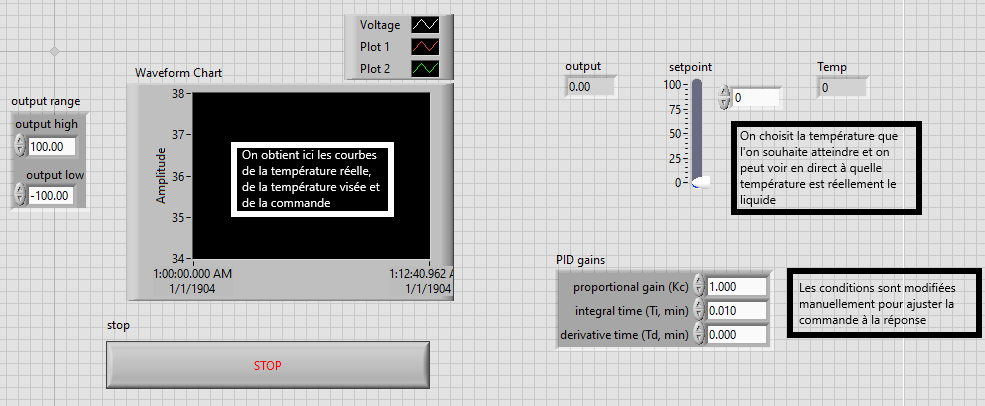
De la plomberie et de l’électricité
Pendant toute la durée du projet nous avons été amenés à réaliser différentes tâches en plomberie et en électricité.
Pour la partie plomberie, nous avons pu changer de nombreux tuyaux, gérer des fuites et surtout éponger le sol !
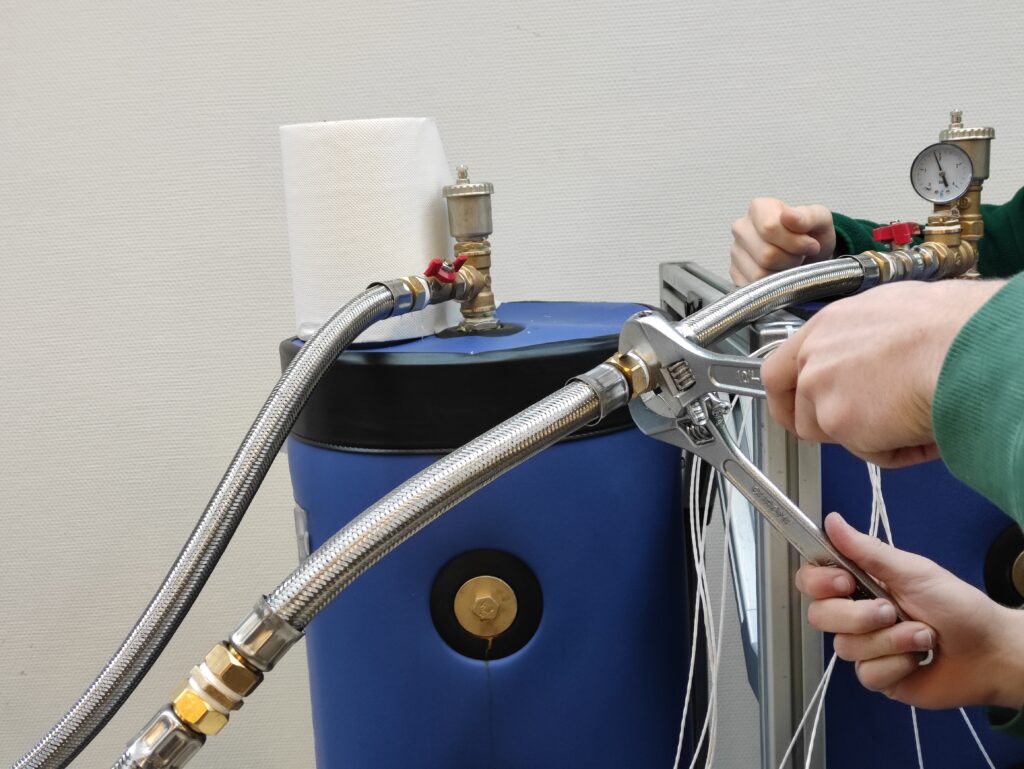
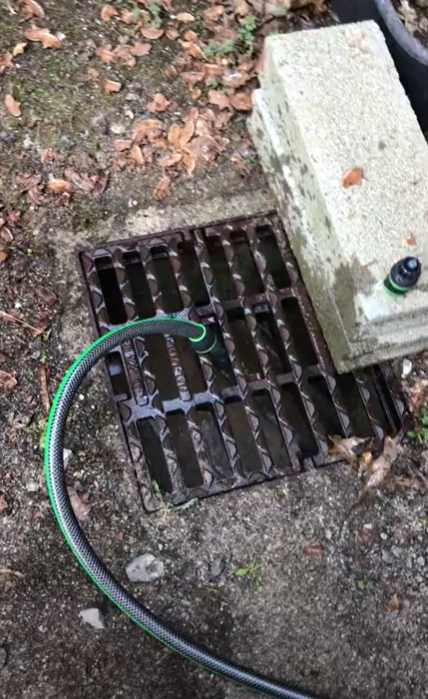
En ce qui concerne la partie électricité, nous avons participé au branchement des cartes NI ainsi qu’à la réalisation d’un relais statique ou encore l’ajout d’un écran sur les débitmètres.
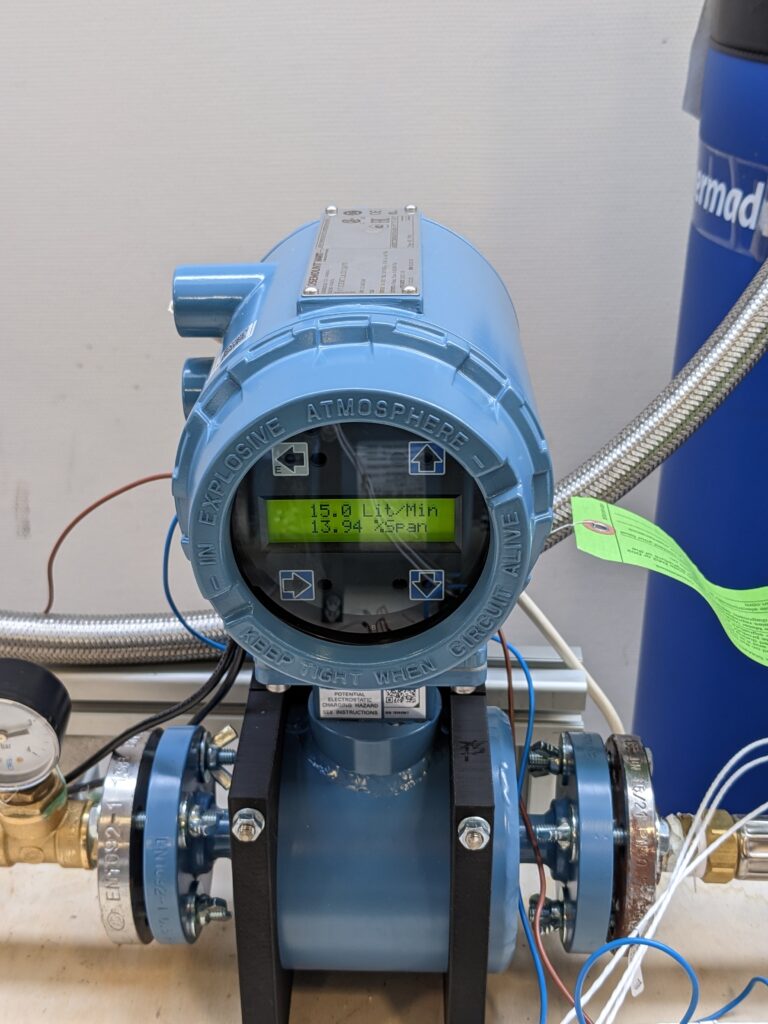
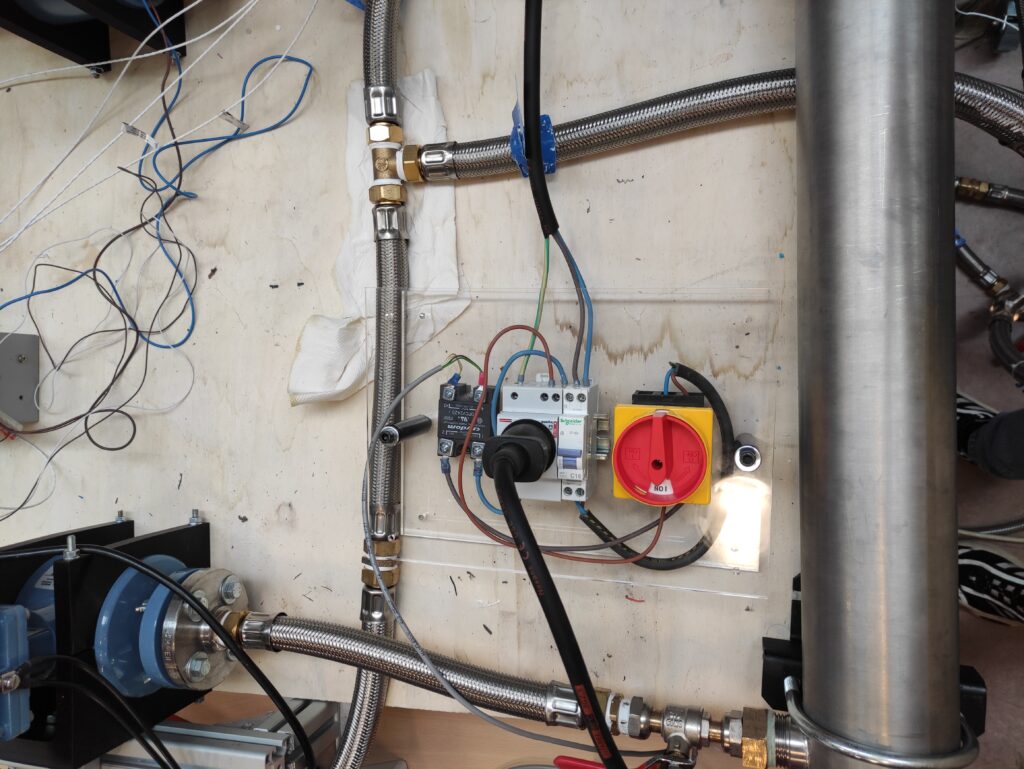
Quels apports pour nous ?
Ce projet a été pour nous l’occasion de développer de nombreuses compétences comme la gestion d’un projet avec les imprévus qui vont avec, l’achat de composants ou encore la pratique de l’anglais scientifique tout au long du projet.
Ce projet nous a aussi permis de visualiser une application directe de la thermique, de l’électricité ou encore de la mécanique des fluides.
Aux étudiants de première année à Polytech Angers, nous vous invitons à choisir un projet comme le notre car cela vous permettra d’effectuer de nombreuses tâches variées dans différents domaines
Merci pour votre lecture !