Présentation
Nous sommes 3 étudiants en PeiP2 à Polytech Angers, et vous présentons à travers ce blog le parcours que nous avons emprunté lors de la réalisation de notre projet : Broie ton plastique.
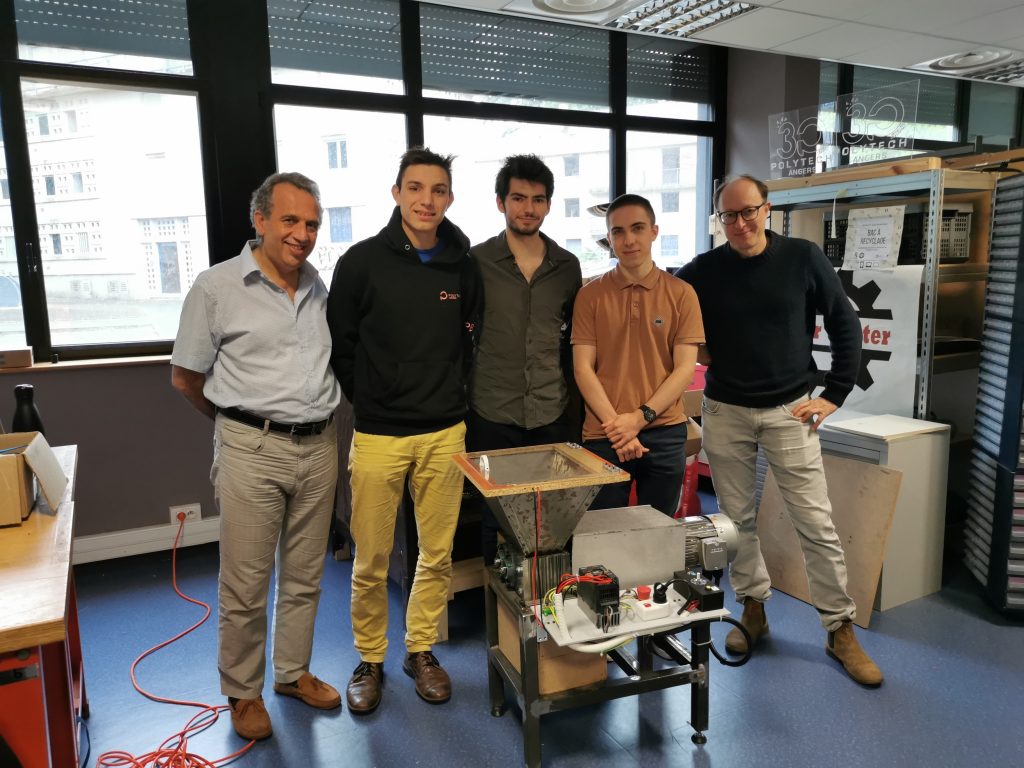
Le FabLab de l’école dispose de nombreuses imprimantes 3D RDM, c’est-à-dire à dépôt de filament, régulièrement utilisées par les élèves lors de TP ou bien pour des projets divers. Ces différentes utilisations génèrent une quantité importante de plastique non exploité par la suite : supports d’impression, rebuts… Le but de ce projet est de revaloriser tous ces déchets, en les broyant pour par la suite pouvoir recréer des bobines de plastique grâce à l’extrudeuse déjà existante au FabLab.
Nous reprenons le projet en cours de création : à notre arrivée, le broyeur est déjà réalisé, le moteur ainsi que son variateur ont déjà été choisis, commandés, et réceptionnés. Notre rôle est de finaliser le projet : concevoir le système de sécurité, le réaliser et tout assembler.
Cahier des charges
Notre mission consiste à rendre le broyeur fonctionnel tout en assurant la sécurité des usagers. Cela comprend : fixer le moteur et le broyeur au bâti, accoupler leurs arbres, intégrer un bouton d’arrêt d’urgence, couper l’alimentation du moteur lors de l’ouverture du capot, concevoir et réaliser un carter pour éviter tout contact avec les arbres en rotation ainsi que l’engrenage, mettre un bouton poussoir à disposition permettant d’actionner le moteur dans le sens opposé afin de pallier les potentiels bourrages du broyeur, et finalement un potentiomètre afin de pouvoir contrôler manuellement la vitesse de rotation du moteur.
Branchement du moteur
Nous disposons d’un moteur qui fonctionne en triphasé : c’est-à-dire qu’il est alimenté par 3 phases contrairement au système de courant monophasé qui lui n’est composé que d’une phase et d’un neutre (le système monophasé est le plus répandu, et alimente certainement votre réseau domestique). Ainsi, pour alimenter le moteur, nous devons utiliser un variateur de tension qui prendra du monophasé en entrée, et sortira du triphasé pour le moteur. Après avoir compris tout ceci, et avec le matériel nécessaire; incluant notamment des câbles de mise à la terre pour protéger l’utilisateur, et plus généralement des câbles suffisamment épais pour supporter la charge de courant; il a suffi de suivre les consignes du constructeur pour procéder au câblage. Une fois cela fait, nous avons pris soin d’ajouter un bouton d’arrêt d’urgence coupant l’alimentation du système si enclenché, ainsi que plusieurs câbles de mise à la terre reliés à la carcasse du moteur, au bâti ainsi qu’au variateur afin de protéger l’utilisateur de potentielles fuites de courant.
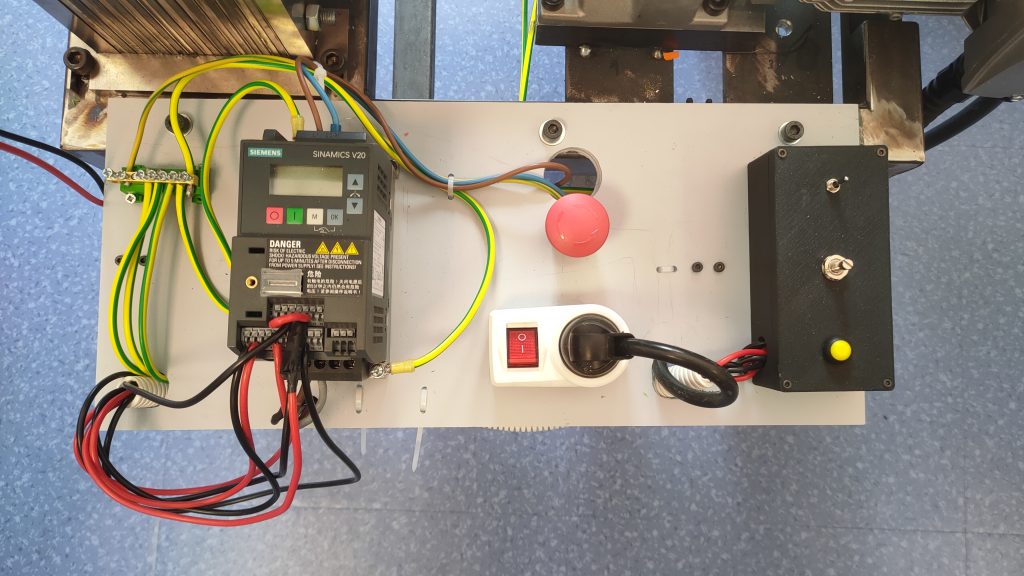
Contrôles du moteur
Le variateur que nous utilisons pour alimenter le moteur est programmable. Il dispose de plus de mille paramètres tous réglable individuellement. Par ailleurs, il propose certaines pré configurations de commande avec un schéma électrique associé. Ainsi, en sélectionnant la configuration la plus adaptée par rapport au cahier des charges, et en connectant tous les boutons aux bonnes entrées et sorties du variateur selon le schéma en question, nous disposons de deux boutons de commande et d’un potentiomètre pour régler la vitesse de rotation. Pour une meilleure présentation, nous avons pris le temps de modéliser et imprimer en 3D un boîtier avec des emplacements pour les boutons, ainsi que des autocollants pour une meilleure lisibilité des commandes.
Protéger l’utilisateur
Afin de protéger l’utilisateur, nous avons mis en place un capot ouvrant au-dessus de l’entonnoir, et en dessous duquel nous avons placé un capteur détectant l’ouverture du capot, afin de couper l’alimentation du moteur s’il est en fonctionnement. Finalement, nous avons conçu un carter de protection en bois afin de cacher les éléments tournant notamment l’engrenage, pour éviter de s’y blesser.
Revalorisation des déchets
Pour finir, nous avons eu l’idée de concevoir un bac de récupération à deux étages, avec une grille les séparant de manière à filtrer les débris à la bonne dimension pour l’extrudeuse. Ceux qui ne conviennent pas pourront subir un nouveau passage au broyeur jusqu’à passer entre les mailles de la grille.
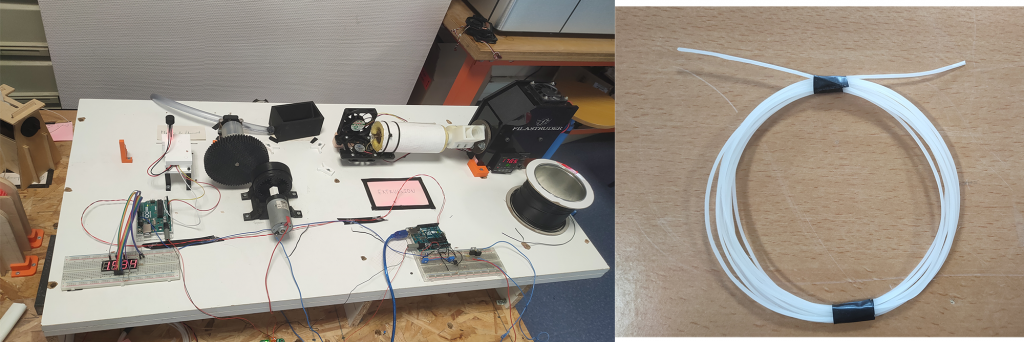
Vous pouvez observer ci-dessus un échantillon de bobine créé par l’extrudeuse, à partir de billes de plastique. Lorsque l’extrudeuse sera de nouveau opérationnelle, nous pourrons exploiter le plein potentiel du broyeur et tenter de recréer des bobines à partir des déchets broyés!
Le meilleur pour la fin
Si vous voulez contemplez le broyeur en fonctionnement, nous vous invitons à consulter la procédure d’utilisation vidéo juste ici :