
Système de stationnement automatique
Bonjour à tous et bienvenue dans notre article.
Nous sommes Maxence, Victor et Margot, trois étudiants en 2ème année du cycle préparatoire intégré de Polytech Angers. Notre projet consiste à concevoir et mettre en place un système de stationnement basé sur Arduino (une maquette d’un parking automatisé). C’est à dire que la barrière s’ouvre et se ferme toute seule quand elle détecte une voiture. Les contraintes sur ce projet étaient de programmer avec Arduino, que le système doive permettre la gestion de stationnement: nombre des places inoccupées qui doivent être affiché sur un écran, la durée de stationnement (en heure) et le prix de stationnement pour chaque voiture garée dans le parking.
Pourquoi avons nous choisie ce projet ?
Nous avons choisie ce projet car il permettait de toucher à tous les domaines : la conception, la programmation, la réalisation, l’impression 3D, etc. De plus, nous ne savions pas quelle spécialité choisir, donc travailler sur ce projet pouvait nous aider dans notre choix.
Étape de notre projet
- Analyse fonctionnelle du système et de ses contraintes
- Recherche de normes sur les vrais parkings
- Recherche sur la maquette (pièces électroniques et planches)
- Programmation sur Tinkercad
- Devis
- Fabrication pièces CAO
- Construction maquette
Première phase: la recherche
Nous avons commencé notre projet par une phase de recherche, nous avons mis en commun nos idées sur le meilleur parking et ce que nous voulions faire. Tout d’abord nous avons fait un schéma fonctionnel pieuvre, que vous pouvez retrouver ci dessous. Grâce a cela nous avons eu une vision des contraintes : l’écologie, le prix, l’esthétique, etc.
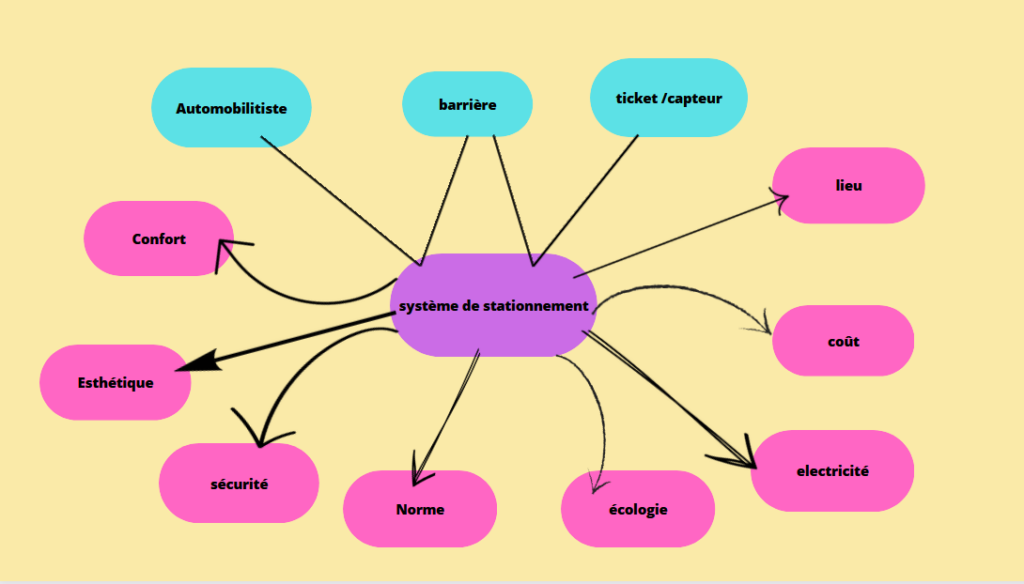
Ensuite nous avons fait un peu de recherche sur la construction d’un vrai parking, afin de respecter au mieux les normes est les dimensions.
La réflexion sur notre maquette
Après ces recherches, nous avons choisi à quoi notre maquette de parking allait ressembler. Nous voulions que le parking ait un étage, deux places handicapées ainsi que deux places électriques. Il y aura 23 places classiques avec une entrée et sortie différente. Les places libres seront indiqué grâce à deux écrans.
Nous avons fait plusieurs devis et commandes d’électronique et de bois pour la structure du parking.
Programmation sur Arduino
Au début nous avons utilisé le logiciel TINKERCAD avons d’avoir les composant. Ce logiciel est un simulateur Arduino avec les composant et la partie programmation. Cela nous a permis de commencé la programmation.
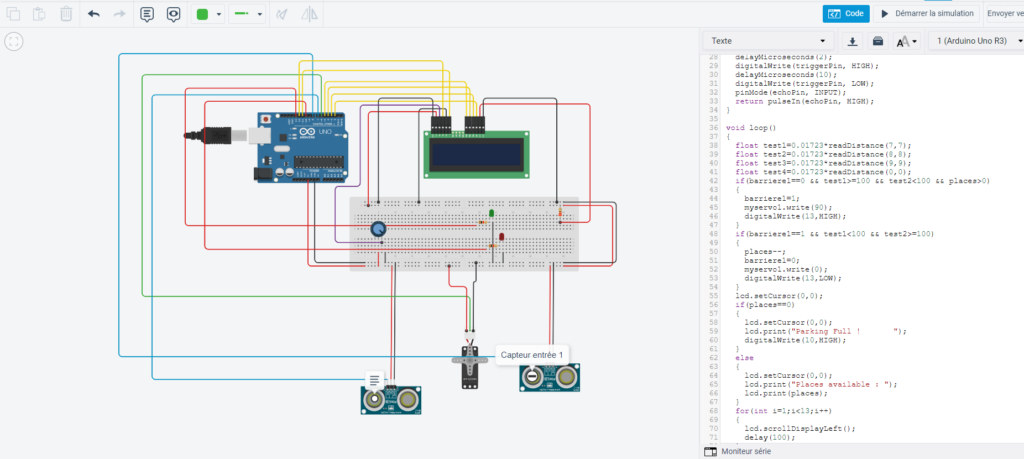
Ensuite nous avons programmé sur Arduino par l’intermédiaire d’une carte Arduino méga.
Conception support 3D
Nous avons principalement utilisé le logiciel SOLIDWORKS, c’est un logiciel de CAO très utilisé à Polytech. Nous y avons construit tout nos panneaux de signalisation ainsi que la barrière et un boitier pour couvrir les câbles et y mettre l’entrée et la sortie. Le point positif avec l’impression 3D est que l’on pouvait vraiment créer les pièces que nous voulions avec les mesures désirées.
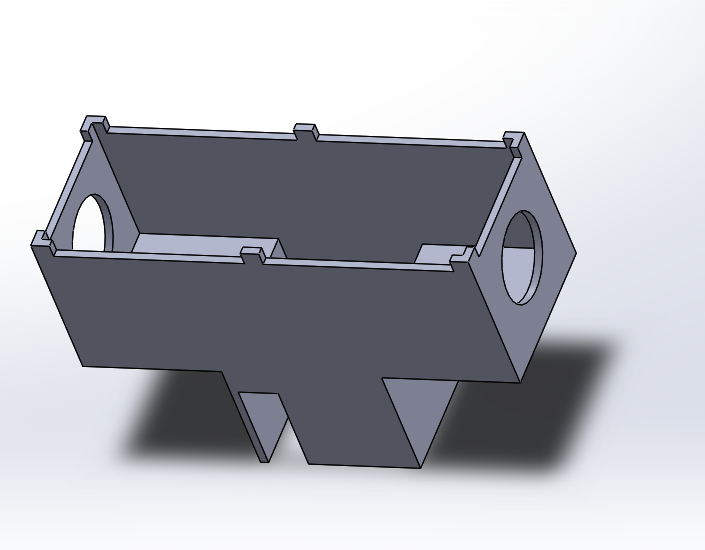
Conception de la maquette
Une fois toutes nos planches reçues, nous avons commencé la construction de la maquette.
La première étape était de tracer toutes les places et passages sur les planches au crayon de bois. Cela nous a permis de voir comment rendait le parking et de faire quelque changement comme agrandir l’espace pour les barrières. Nous avons fait cela sur les deux planches.
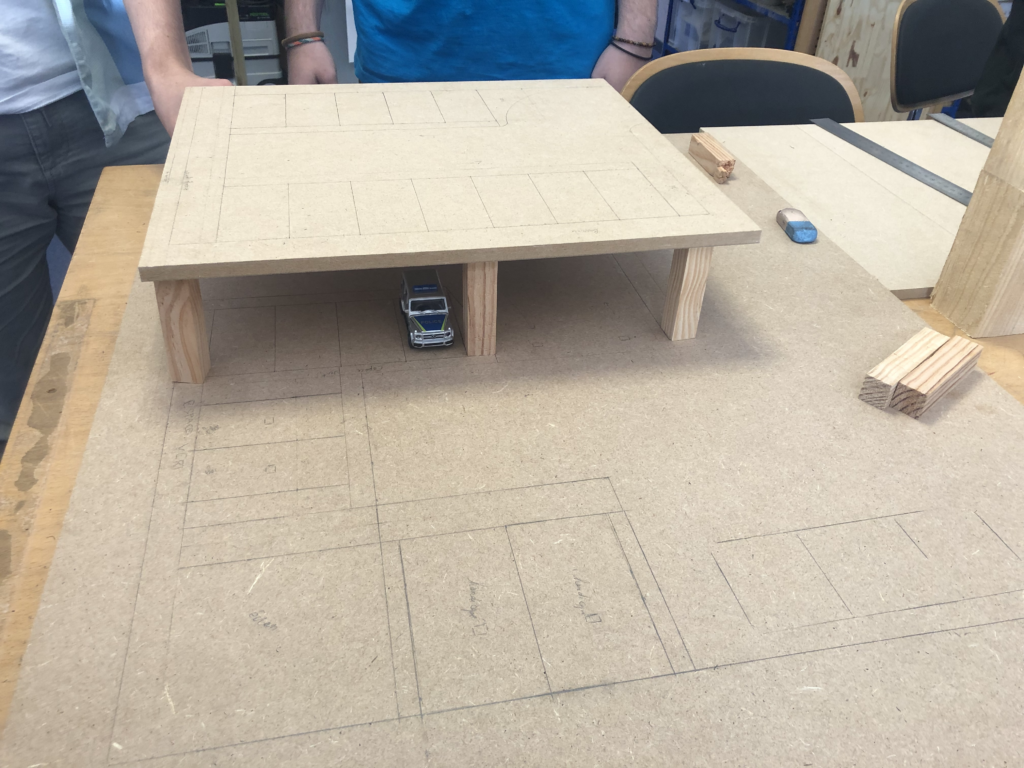
Ensuite nous avons dimensionné et coupé les poteaux permettant de surélever le parking et de créer l’étage.
Après nous avons installé les capteurs et écrans (toutes l’électronique). Nous avons décidé de faire passer tous les fils sous la maquette pour que le rendu soit plus propre. Donc il a fallu faire plusieurs trous pour faire passer les capteurs.
En parallèle, nous avons imprimé les panneaux 3D ainsi que les barrières de protection et les barrières d’ouverture. Nous avons aussi créé des cartes de différentes couleurs avec des planches de bois et des stickers que nous avons conçu. Ces cartes vont permettre d’être reconnues par les capteurs couleur à l’entrée et à la sortie du parking, cela permet de simuler les cartes d’abonnement d’un parking réel.
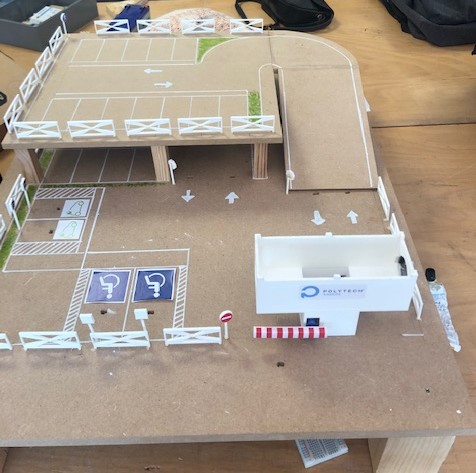
Pour finir, nous avons tout fixer : les piliers sur l’étage, panneaux, barrière et toute la partie électronique, ainsi que repasser au crayon Posca tous les marquages. Notre maquette est prête ! Maintenant c’est le moment de tester. Nous vous avons mis ci-dessous une vidéo du fonctionnement complète de la maquette.
Merci à vous !!!