Bonjour à tous, ce blog a pour but de vous présenter l’avancement de notre projet réalisé durant notre 4ème semestre du cycle préparatoire Peip à Polytech Angers. Nous sommes 4 acteurs sur ce projet, 3 étudiants ainsi qu’un professeur référent. L’objectif de ce projet est, comme son nom l’indique, de réaliser un automate animé. Celui-ci aura pour but de réaliser un mouvement naturel automatisé, et sans assistance extérieure.
1 – Le choix de notre automate
Tout d’abord, il a fallu choisir l’animal, l’objet à animer. L’idée d’un animal quadrupède nous est directement venue à l’esprit. N’étant pas le premier groupe à travailler sur ce projet, nous avons eu quelques sources d’inspiration. Je vous invite à aller regarder leur blog ainsi que leur compte-rendu, car certaines idées y sont reprises tandis que certaines erreurs y ont aussi été comprises. Chaque groupe s’est inspiré de l’ancien pour faire évoluer la qualité de ce projet. Pour revenir sur le choix de notre automate, Disney a aussi été une source d’inspiration étant donné que l’idée de ce projet vient de leur vidéo sur le sujet.

Nous avons donc eu l’idée de partir vers le chien ou le chat, mais cela nous a paru trop classique. Nous avons donc pensé au dragon. Il a exactement les mêmes articulations que le chat. Cette démarche s’en rapproche donc énormément. Il sera donc facile de pouvoir modéliser son mouvement.

2 – Modélisation du premier prototype
Pour commencer, nous avons dû modéliser le premier prototype de notre automate. Cela était une des parties les plus complexes de ce projet. Nous avons donc commencé par modéliser la patte arrière de notre automate, en s’inspirant d’un prototype de Disney.
Le plus difficile a été de trouver les bonnes dimensions de chaque bielle ainsi que le placement des différentes roues pour trouver le mouvement de la patte voulue.
3 – Découpe et Assemblage du 1er prototype
Nous sommes ensuite passés à nos premiers tests, pour imprimer notre prototype nous avons utilisé la découpeuse laser présente au FABLAB. Pour l’utiliser, nous avons mis sur plan toutes nos pièces puis ajuster les bons paramètres de matériaux.
4 – Modélisation fonctionnelle de l’automate
Notre premier prototype étant fonctionnel, nous sommes passés à la modélisation de notre automate entier sur CAO sans nous soucier de son apparence.
5 – Amélioration du design
Après avoir modélisé notre automate fonctionnel, nous avons essayé de le rendre plus esthétique et de donner une forme plus réaliste aux différentes pièces.
Avant / Après :
Nous avons également testé différentes manières pour graver des écailles sur nos pattes.
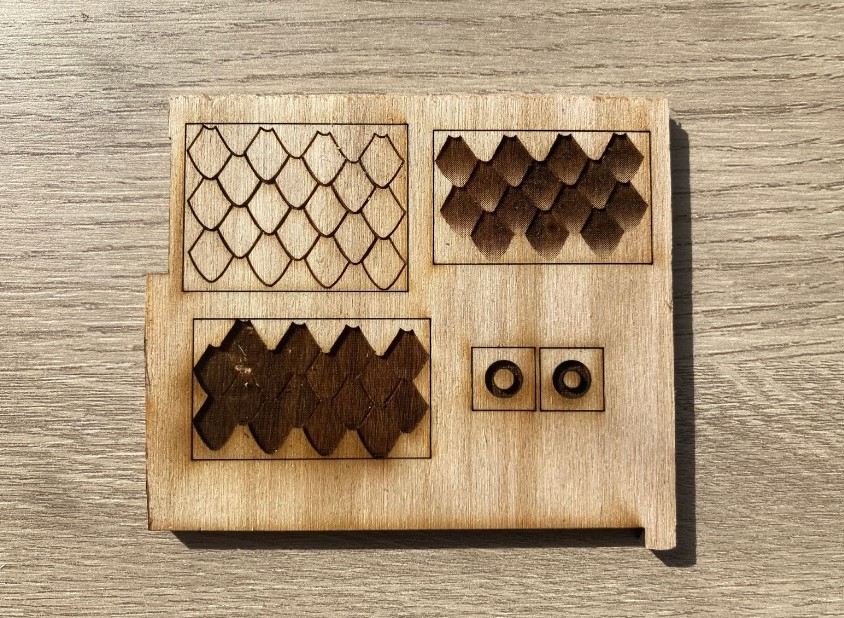
6 – Modélisation et ajout des ailes
Pour ajouter un côté plus réaliste, l’ajout d’ailes au dragon était nécessaire. Pour ce faire, nous avons directement imaginé le mécanisme pouvant animer ses ailes pour le biais d’une roue engendrant une bielle qui elle-même met en mouvement l’aile. L’aile est quant à elle fixée par un support au corps de l’automate. Cette fixation permet de laisser pivoter l’aile sur l’axe voulu.
Nous avons ensuite donné un design à l’aile pour la rendre plus jolie.
7 – Découpage et gravure de l’entièreté des pièces
La prochaine étape pour nous était l’impression et la gravure de toutes nos pièces qui nous prit tout de même plusieurs heures.
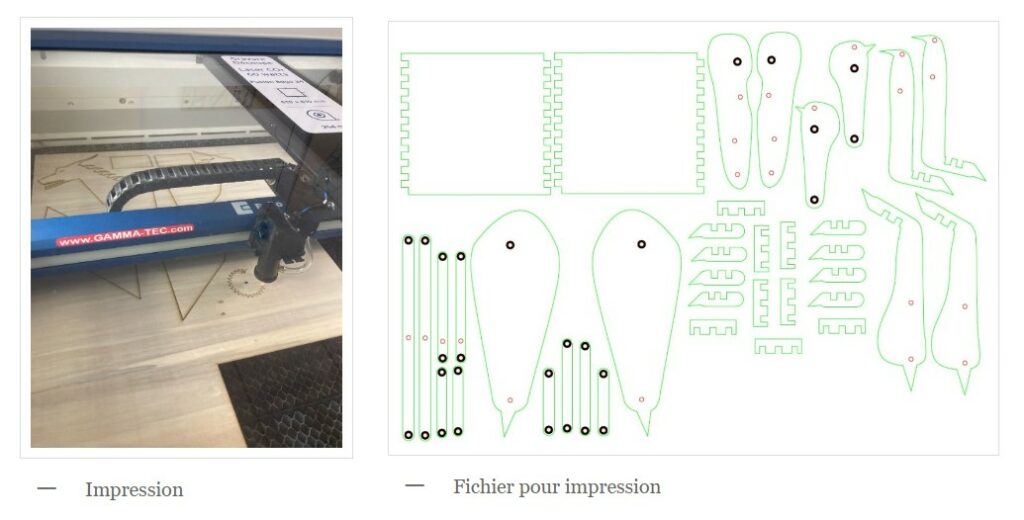
8 – Assemblage final de l’automate
La dernière partie de ce projet aura été l’assemblage de l’automate en entier. Il nous a d’abord fallu assembler les 6 parties constituant le corps.
Pour ensuite y ajouter les pâtes et les ailes. Entre temps, nous avons dû assembler l’ensemble des pattes avant et arrière avant de les lier au corps et aux engrenages.
La partie la plus dure de l’assemblage a été de lier le mouvement des engrenages avec le mouvement des roues comme vous pouvez le voir sur la photo ci-dessous.
Par la suite, il a fallu rajouter le mécanisme des ailes ainsi que les ailes elles-mêmes. L’assemblage des ailes était la partie la plus simple, elle est la seule à ne pas nous avoir causé de soucis.
Enfin, pour finir, il suffit de coller la tête sur le corps de notre dragon pour qu’il en soit vraiment un !
9 – Conclusion
Pour conclure, ce projet a été très intéressant et complet pour nous, en découvrant l’avancement de celui-ci, de sa création à sa réalisation. Il nous a permis d’utiliser une multitude de technologies de la CAO au simple tournevis en passant par la découpeuse laser. Malheureusement, nous n’avons pas réussi à le motoriser comme voulu au départ. Cela est dû au matériau choisi pour le corps de l’automate. Le bois utilisé étant trop souple, il ne nous a pas permis de fixer suffisamment la roue des pattes à leur engrenage, résultat de pattes non entraînées par le mouvement des engrenages. Cependant, nous sommes quand même fiers d’avoir pu créer un automate fonctionnel même si très fragile.
Merci d’avoir pris le temps de lire notre blog
Robin JEULAND, Quentin CONANEC, Clément LE GALL