Vous en avez marre que vos enfants passent trop de temps devant les écrans? Vous voulez construire vous-même une voiture télécommandée de A à Z? Nous avons ce qu’il vous faut.
Bonjour à toutes et à tous;
Nous sommes un groupe de trois étudiants composé de Clément Bouaud, Thomas Creusier et Erwan Gémard. Nous sommes tous les trois intéressés par la modélisation, de plus l’un d’entre nous est passionné par le domaine de la programmation et les deux autres par celui de la mécanique. Ce projet était celui qui nous correspondait le plus.
Alors, quel est ce projet ?
Notre projet était la réalisation d’un nouveau châssis pour une voiture à air comprimé. Nous avons donc décidé de partir sur un châssis pouvant apporter quelque chose en plus vis-à-vis du châssis original.
Quelle est l’utilité de notre projet ?
Nous avions à l’initiale un cahier des charges nous orientant vers la création d’un nouveau châssis pour la performance de la voiture. Or après discussion avec notre prof référant, nous avons changé certaines lignes du cahier des charges pour qu’il puisse mieux nous correspondre. C’est pourquoi nous sommes partis sur un châssis plus grand pouvant intégrer de nouvelles fonctionnalités comme une direction ou l’annexion de la pompe. L’ancien châssis étant assez impersonnel et trop “banal”, nous avons modélisé un châssis qui nous plaît bien plus et qui est plus attirant visuellement que l’ancien.

Les objectifs principaux
- Modifier intégralement le châssis; partant d’un châssis assez petit et fragile, il fallait créer un châssis solide pouvant accueillir plus de composants.
- Créer une direction motorisée; pouvoir diriger la voiture en Bluetooth avec une direction d’environ 30° de chaque côté.
- Remplacer l’ancienne pompe (cassée); pouvoir pomper et compresser l’air dans une voiture à air comprimé, c’est plutôt utile!
- Créer de nouveaux tuyaux en dur; un des plus gros problèmes de l’ancienne voiture était ces tuyaux mous très fragiles puisqu’il cassait d’un rien, les rendre durs était donc une nécessité.
Le début et les première idées
Nous avions plusieurs inspirations pour le futur design, comme une Batmobile ou encore une 2CV. Mais celle qui fut retenue est le visuel d’une formule 1. Grande, plate, spacieuse et surtout facilement aménageable pour nos composants. Voici ci-dessous les premières esquisses du visuel:
Transformation en 3D
Nous nous sommes partagés les tâches de manière à être plus efficace en commençant par l’avant de la voiture pour finir par l’arrière. Ainsi la première pièce réalisée fut le nez de la formule 1, aucune utilité pour l’aspect technique mais importante pour le design de la voiture.
Ensuite nous avons commencé à désigner la partie électronique avec la direction. Tout le bloc avant est dédié à cette partie-là et uniquement à celle-ci. Dessus est fixée la carte Arduino avec son Shield et le module Bluetooth; l’alimentation; le moteur pas à pas et la direction.
Pour continuer, la modélisation de tout le train arrière fut assez simple pour pouvoir quant à elle accueillir la partie air comprimé. Elle permet donc de fixer la bouteille et de pouvoir la relier au système d’air créer via des tuyaux modélisés.
L’air est pompé via une pompe annexe possédant un manomètre. Le circuit d’air est donc composé d’une valve à vélo relié à la bouteille servant de réservoir et aux deux valves des pistons.
Le temps des impressions
Nous avons donc dû imprimer toutes nos pièces modélisées sur des imprimantes 3D. Ce fut une partie très fastidieuse puisque nous avons au total plus de 50 heures d’impression. Avec une pièce allant jusqu’à 22h d’impression à elle seule (pièce noire sur la photo). La qualité de certaines pièces est à revoir mais nous avons dû parfois sacrifier la qualité pour avoir le temps de tout imprimer.
L’assemblage de chaque partie
Nous avons préféré percer directement sur la CAO pour avoir la bonne forme hexagonale (pour caler les écrous) et pour percer la bonne longueur vu que nous avons seulement 4 tailles de vis (15,20,30,40 mm). Nous devions donc comprendre comment fixer efficacement les pièces entre elle sans fragiliser celles-ci tout en ayant une force de maintient assez importante. Or certaines pièces n’avaient pas la place nécessaire donc nous les avons coller avec soit de la glue, soit de la colle chaude. En général ce n’étaient pas des pièces ayant un fort effort mécanique (ex: l’aileron arrière). De plus, certaines pièces ont été avec un encastrement parfait, à 0.1 mm près. Or les imprimantes 3D n’impriment pas avec une telle précision donc nous avons dû retailler des pièces ou les passer dans l’eau chaude pour les ramollir.
L’électronique et le codage
Nous avions comme idée de créer de toutes pièces une direction commandable à distance via le Bluetooth et un moteur pas à pas. La commande effectuée sur le portable de l’utilisateur envoie un signal à la carte Bluetooth de la voiture qui donnait un ordre au moteur et ainsi tourne d’environ 30° la direction (à droite ou à fauche bien entendu). Malheureusement nous avons eu des contre-temps qui nous ont empêché de finir cette partie, nous allons vous expliquer pourquoi.
Les problèmes et difficultés rencontrés
Au début du projet nous n’avons rencontré aucun réel problème si ce n’est que celui de trouver de l’inspiration pour pouvoir designer la voiture. Les problèmes arrivent environ vers le milieu du projet lorsqu’il a fallu commander les pièces pour notre projet, comme le moteur pas à pas ou la valve de vélo. Nous avions envoyé des liens de pièces correspondant à nos besoins mais pour un problème au niveau des sites envoyés nous avons dû en rechercher des nouvelles. Puis nous avons perdu plus d’un mois suite à une absence de notre professeur référant qui faisait le lien entre nous et le service de commande de Polytech. Suite à ça, lorsqu’il est revenu nous n’avons pas pu échanger avec lui puisque étant responsable du département QIF il devait gérer d’autres priorités. Nos pièces n’étant donc pas commandées nous avons commencé à ralentir le rythme au niveau de la modélisation puisque nous avions besoin des pièces pour pouvoir finir cette dernière. En ayant accumulé tout ce retard alors qu’ils ne nous restaient plus que 5 séances, nous avons décidé de bricoler pour certaines pièces et pour la fixation des pièces. Nous avons donc pu obtenir au final le design presque final de notre châssis (absence du moteur pas à pas, de la valve de vélo et des joints). Malheureusement il n’est pas fonctionnel au vu du manque des pièces importantes.
Conclusion
Pour terminer cet article, nous avons adoré travailler sur ce projet malgré les problèmes rencontrés. Celui-ci nous à aider à mieux comprendre tout le développement que nécessite une pièce aussi importante qu’est le châssis dans un véhicule. Il nous a permis de nous entraîner et nous améliorer en CAO sur SolidWorks. La finalité de ce projet se traduit par la création entière de ce nouveau châssis qui est fonctionnel pour rouler en la poussant sur quelques centimètres.
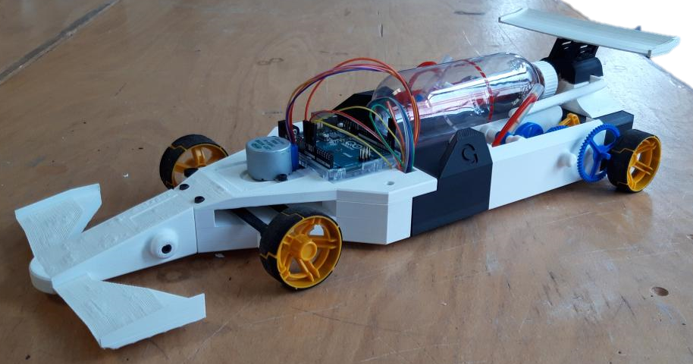
Clément BOUAUD, Thomas CREUSIER, Erwan GÉMARD