« Développer » est la deuxième compétence que nous devons acquérir. Avec ce savoir-faire, nous sommes capables d’identifier et proposer des solutions technologiques optimisées et innovantes, dans le but de répondre aux attentes et besoins des clients, qui n’ont de cesse de vouloir faire évoluer leur produit et/ou leur chaine de production avec pour finalité d’être encore plus compétitifs.
Pour mettre en pratique cette compétence, nous avons été mis en situation avec les projets des :
- SAÉ 2.2 « Implantation d’un ilot robotisé de production »
- SAÉ 2.23 « Conception d’une pièce de sécurité – Conception, optimisation de la forme et fabrication d’une biellette »
.
Les compétences visées sont :
- Situer les éléments d’un système simple et leurs interactions, dans l’espace, dans le temps
- Interpréter les spécifications en fonction de leur représentation pour un système simple
- Choisir des solutions appropriées pour des cas simples en étant accompagné / guidé
L’objectif de la SAÉ 2.2 était de proposer plusieurs solutions d’implantation dans une ligne de production, en remplacement d’un robot obsolète, en intégrant les besoins de tous les métiers / services concernés.
Quant à l’objectif de la SAÉ 2.23 il s’agissait de concevoir et de fabriquer une pièce de sécurité, une biellette en l’occurrence, pour laquelle nous devions présenter une forme optimale permettant de limiter les concentrations de contrainte traction / compression.
Interpréter les spécifications en fonction de leur représentation pour un système simple
SAÉ 2.23
Dans la SAÉ 2.23, notre principale mission était de concevoir et fabriquer une biellette qui sera soumise à des sollicitations de traction / compression.
La pièce doit être fabriquée à partir d’une plaque de dimension : 150 x 25 mm et d’épaisseur 1 mm.
Les propriétés élastiques du matériau sont définies par : e= 250 MPa, E=210 GPa et v = 0.3.
Contraintes techniques
- La pièce doit résister à une charge de 700 N.
- Le coefficient de sécurité choisi pour cette pièce est égal à 3.
- Le nombre de pièces à réaliser est de trois
- La biellette doit être la plus légère possible.
- L’entraxe D doit être entre 125 à 128 mm, le diamètre de chaque trou est égal à 10 mm.
Choisir des solutions appropriées pour des cas simples en étant accompagné / guidé
SAÉ 2.23
Pour cette SAÉ, un brevet a été déposé auprès de nos professeurs référents, afin de valider la solution adéquate.
Cinq grandes idées se sont démarquées et ont été dessinées, afin que nous puissions les analyser et réfléchir à leur potentiel. Les quatre premières hypothèses n’ont pas été retenues, car elles n’étaient pas exploitables et/ou ne répondaient pas aux impératifs de fabrication.
La 5ème hypothèse a été validée par nos référents. Il s’agissait d’une conception de forme ovale, car nous voulions créer une biellette originale, avec une épaisseur de 1mm, comme il était indiqué dans nos consignes.
Celle-ci répondait à tous les critères (perdre de la matière et de la masse, avoir une géométrie originale) et nous permettre après brevetage (géométrie) de la modifier pour réduire au maximum sa masse. Nous avions arrondi les bords aux extrémités et avions fait des trous oblongs pour gagner de la masse.
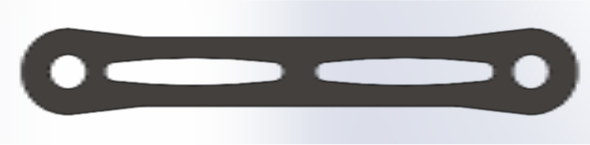
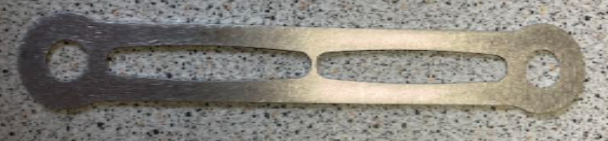
SAÉ 2.2
Dans cette SAÉ, nous devions remplacer un robot obsolète par un, voire deux, robots du catalogue FANUC.
Pour faire notre sélection, nous avons dû prendre en compte, entre autres de l’emplacement du robot, l’accessibilité aux différents points de prise/dépose de la ligne de production, ainsi que le poids minimal qu’il doit supporter.
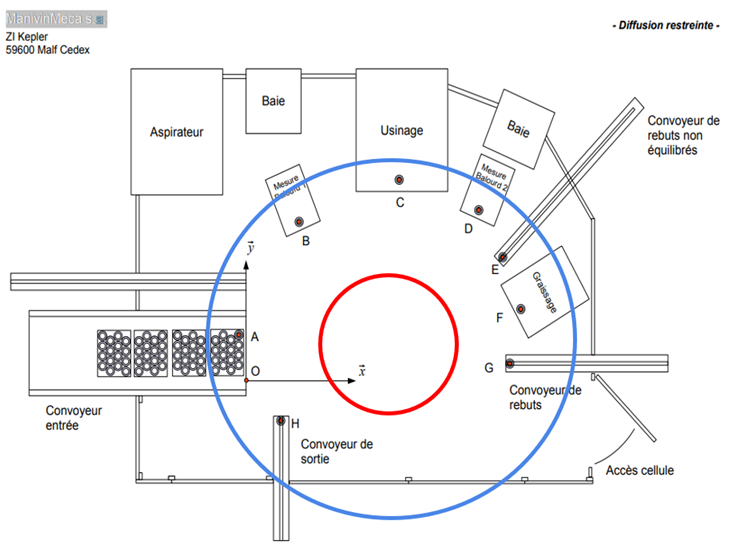
A partir de toutes ces données, nous avons pu faire notre recherche dans le catalogue FANUC, qui propose différents modèles, d’après des fiches détaillées. Notre sélection s’est tournée vers le modèle 3 Série M-10 version iD type 12, car il répond le plus aux attentes et besoins du client et aux contraintes de la chaîne de production.
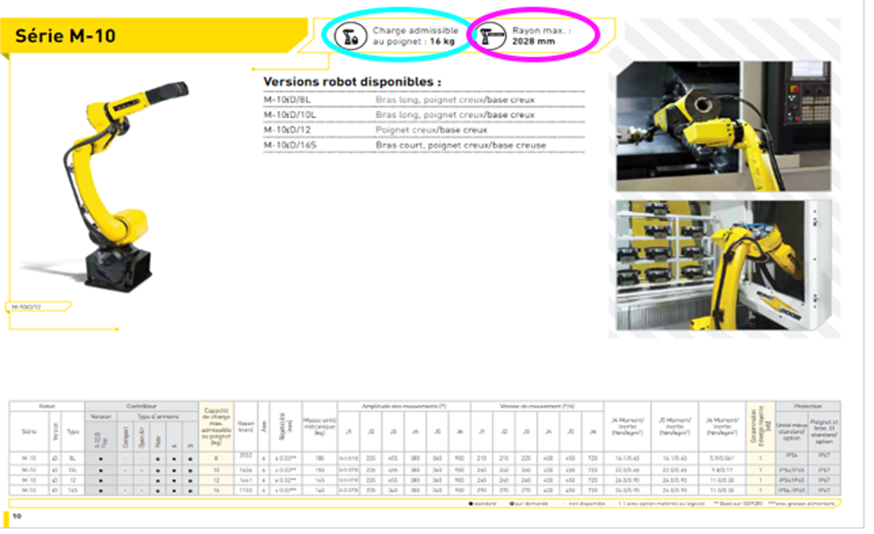
Nous avons effectué le même exercice, mais avec l’implantation de deux robots dans la cellule.
Nous avons opéré de la même manière, nous avons déterminé le rayon d’action de chaque robot, l’accessibilité à chaque point de prise/dépose, ainsi que le poids minimal qu’ils doivent soulever…

De nouveau, nous nous sommes appuyés sur le catalogue FANUC et nous avons sélectionné les robots Scara.
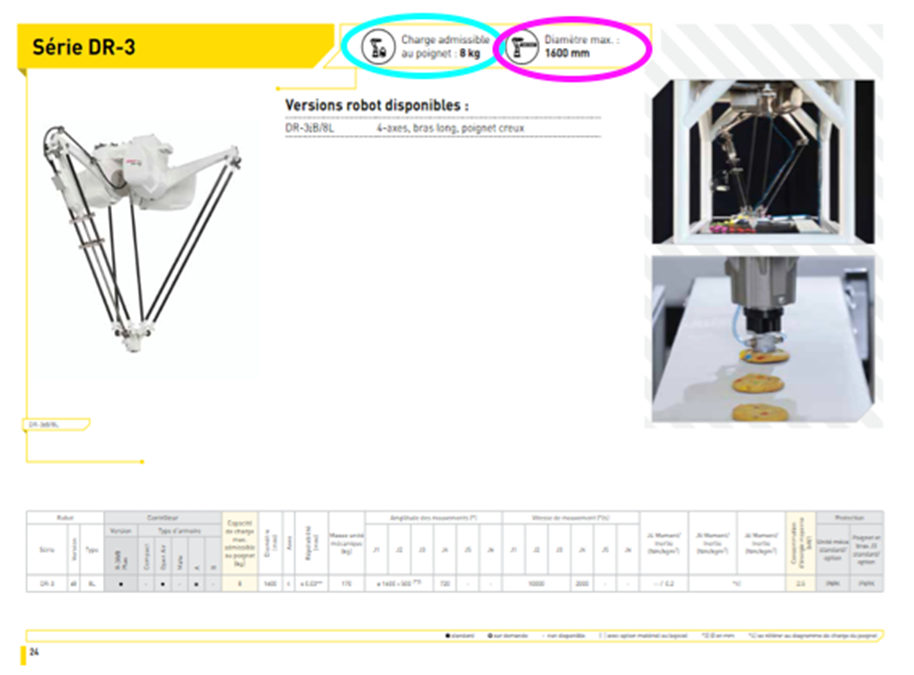
SAÉ 2.23
Nous devions déterminer une solution conceptuelle d’une biellette ayant une géométrie qui permet un gain de matière et une perte de masse.
Après avoir validé la forme de la biellette, nous devions définir le choix du matériau et le procédé de fabrication.
- Pour le choix du matériau
Le groupe s’est concerté, afin de chercher un matériau qui puisse répondre aux critères qui nous ont été donnés : module de Young E = 210 GPa, la contrainte élastique contrainte e = 250 MPa, ainsi que le coefficient de poisson V = 0.3.
Les deux principaux matériaux que nous avions sélectionnés sont l’aluminium et l’acier. Pour faire notre choix, nous avons cherché à savoir lequel de ces deux matériaux serait le plus avantageux en rapport masse résistance. L’acier nous a semblé être la meilleur solution, car sa résistance est trois fois plus élevée que celle de l’aluminium. Nous nous sommes donc orientés sur une “tôle 1023 acier au carbone SS” pour les simulations SolidWorks.
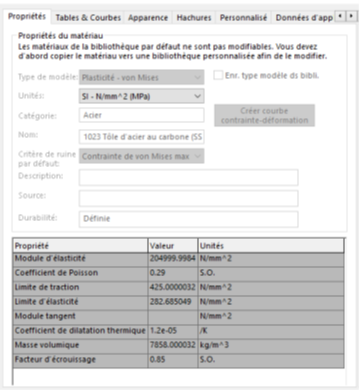
Modélisation et étude statique
Voici la biellette avec une force traction de 700 newtons. Il y a une contrainte maximale de 7.581e+01 MPa.
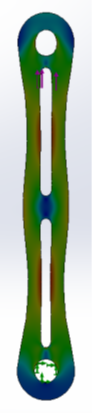
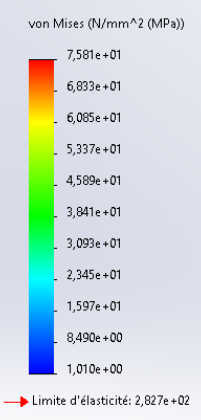
Modification éprouvette pour mise dans les mors :
Nous avons optimisé la biellette, c’est-à-dire que nous avons cherché à perdre de la masse en reprenant la géométrie brevetée, pour se rapprocher de la masse requise 16 gr.
Nous avons effectué des modifications sur les extrémités de la biellette, afin qu’ils puissent se loger dans les mors, spécialement conçus pour cette pièce. Il s’agit du moyen de mise en position de la biellette dans la machine d’essai de traction. Sans cette étape, la biellette n’aurait pas pu être exploitable, car elle aurait été dépourvue de moyen d’accroche dans les mors.
Contraintes géométriques
§ Partie zone en prise dans les mors :
§ Longueur : 25 mm
§ Largeur : 25 mm
§ Perçage de ⌀6mm centrer au milieu du carré de 25 mm
§ Taille maximale de 180 mm
Modélisation et étude statique :
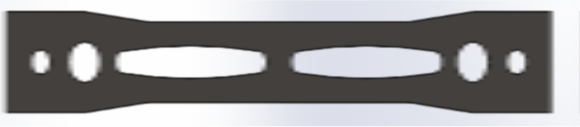
Voici la biellette avec accroche pour les mors en traction avec une force de 700N

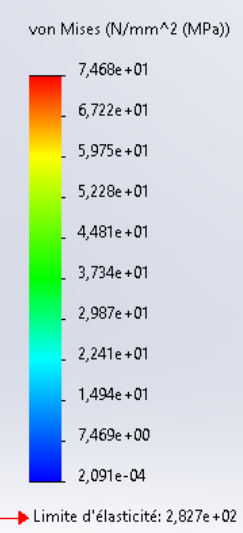
- Procédé utilisé
Pour la conception, nous avons dû utiliser le découpeur plasma, cette méthode était requise par les encadrants de la SAÉ. La découpe plasma est un procédé de découpe par fusion (localisée), dans laquelle un jet d’air comprimé ou de gaz chasse le métal. Dans notre cas, l’acier est porté à une température de fusion. La température générée par l’arc électrique peut atteindre les 18 000°C.
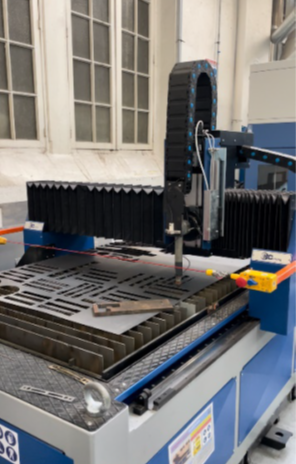
Résultats essais de traction
Nous avons ensuite utilisé nos trois biellettes, de manière à effectuer trois essais de traction et observer leur réaction.
Nous avons pu constater que les trois essais de traction n’ont pas été identiques, car les contraintes maximales que nous avons pu atteindre n’ont pas été les mêmes et de très loin. Selon les différents graphiques émis par PROCAM, il y a une différence d’environ 400 N entre chaque biellette.
Nous avons pu aussi remarquer que les trois ruptures ne se sont pas produites au même endroit.
Nous avions émis l’hypothèse que les biellettes ont été fragilisées à cause de la chaleur et lorsqu’elles sont tombées durant leur conception, particulièrement la dernière qui était courbée.
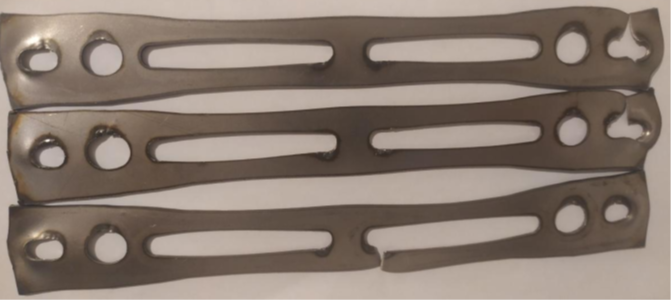
Nous avons pu constater que le contrôle dimensionnel du prototype présentait des imperfections par rapport à la simulation sur SolidWorks, qui modélisait la pièce parfaite.
Nous avons eu une déformation moyenne des trois essais de 1.8 mm, ainsi qu’une contrainte moyenne de 298.23MPa.
Lorsque l’on utilise une machine, il faut tenir compte qu’il y a toujours une petite marge d’erreur.
La pièce réelle résiste à une force maximale de 3 200 N pour la moins bonne, jusqu’à 4 000 N pour la meilleure.
SAÉ 2.2
Dans cette SAÉ, nous devions modifier la ligne de rectification de pignons d’une société, en remplaçant un robot obsolète par un, voire deux, robots du catalogue FANUC.
Nous avons eu besoin de tenir compte de plusieurs facteurs pour faire notre choix :
- La masse d’une pièce traitée par la ligne de production : 0,198 kg
- La disposition des pièces : elles seront stockées par 16, disposées en quinconce dans des bacs plastiques.
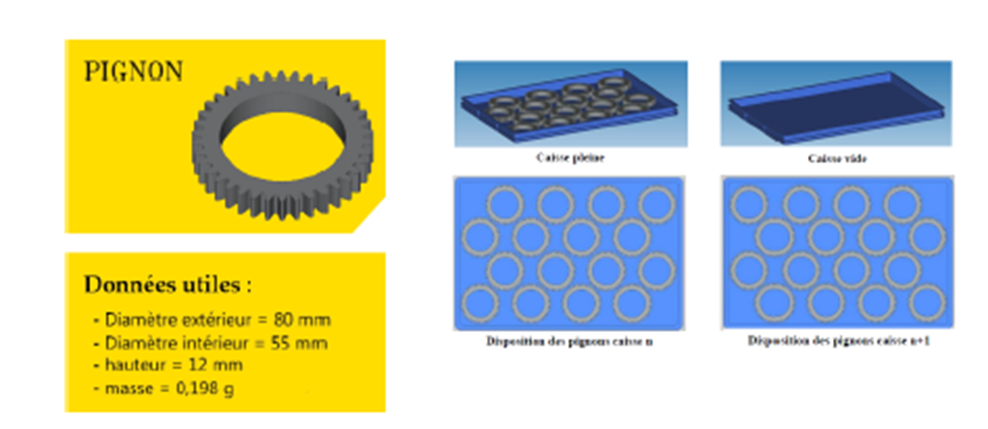
Les étapes de la ligne de production
- Les pignons arrivent dans les bacs sur le convoyeur d’entrée
- Ils subissent une mesure de balourd initial dans la machine ‘Mesure Balourd 1’ au point B.
– si les mesures sont hors-tolérance, la pièce est évacuée, sur le convoyeur ‘Rebut
pièces non équilibrées’ au point E
- Sinon, le pignon est réusiné au point C dans la machine ‘Usinage’ à partir des données de mesure
- Un dernier contrôle de balourd résiduel est réalisé dans la machine ‘Mesure Balourd 2’ au point D
- En fonction des résultats de cette dernière mesure, la pièce est évacuée :
- vers la machine de graissage au point F puis sur le convoyeur de sortie au point H si
les mesures sont conformes
- sur le convoyeur de rebuts au point G si le balourd résiduel est non conforme
- Les pignons devront être présentés face supérieure vers le haut pour tous les points de prise/dépose. Cette seule face est usinée dans la phase de reprise de balourd
Définition implantation
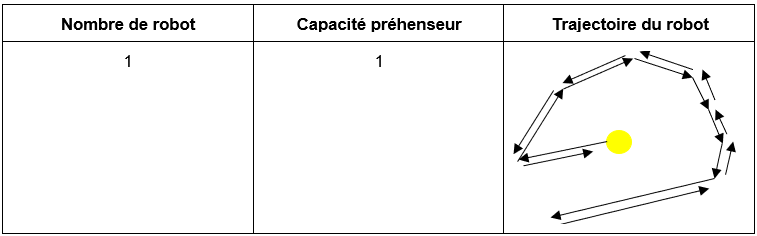
Cycle de traitement
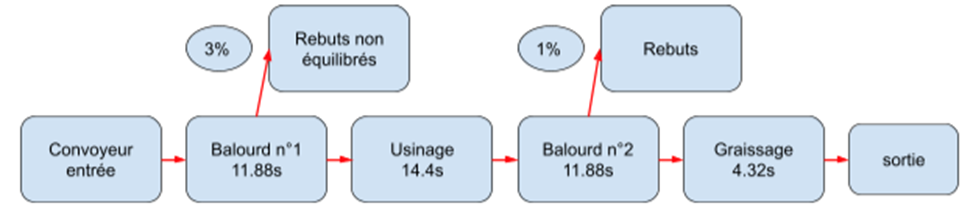
Opération robot
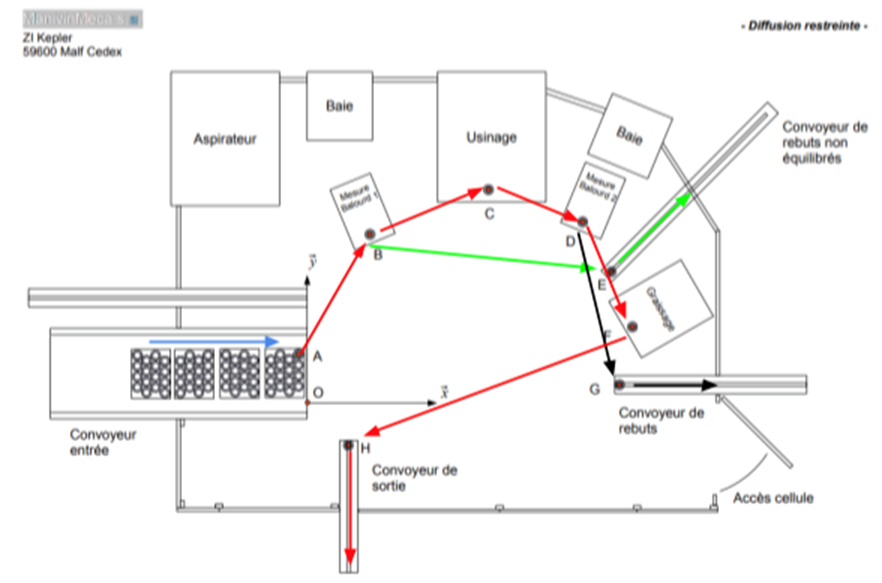
Nous avons eu besoin également d’utiliser des mesures permettant d’établir les positions des points de prise/dépose.
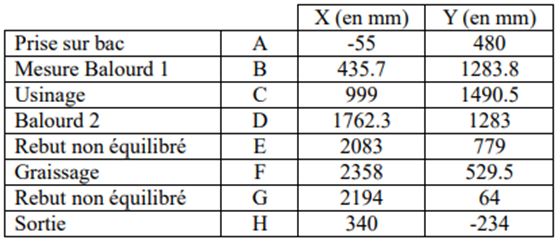
L’ensemble des points de prise/dépose ont été mesurés à une hauteur de 1 200 mm du sol fini.
Pour déterminer le choix du robot, nous avons dû tout d’abord regarder le rayon d’action minimum de celui-ci.


Cette donnée sur x, nous a permis de savoir quel rayon minimum était à choisir, si l’on voulait installer un seul robot au centre de la cellule.
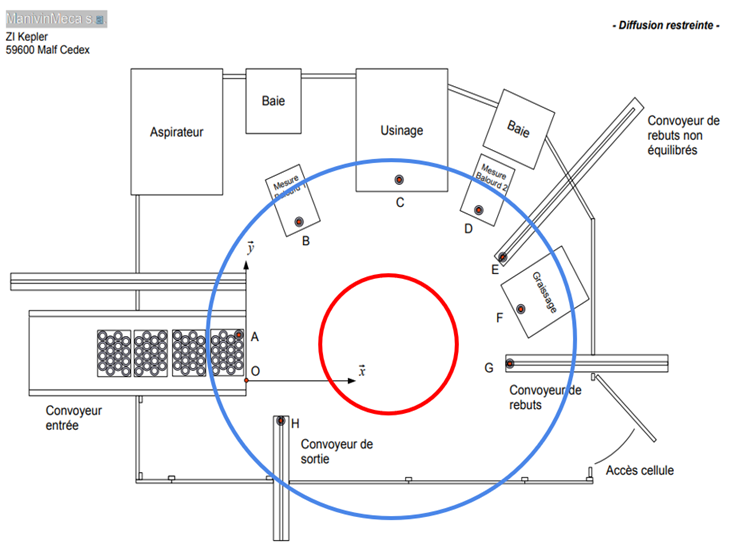
La zone en rouge ci-dessus était l’emplacement du robot.
La zone en bleu était sa zone d’action. Nous avons pris un rayon d’action légèrement supérieur à 2 413 mm, pour permettre à notre robot situé dans la zone rouge, d’atteindre chaque point de position de nos pignons (en rouge sur la cellule).
Après avoir déduit les zones d’actions d’une cellule, dans le cas où il y aurait un seul robot, nous avons cherché dans le catalogue des robots FANUC, le robot qui répondait à nos critères, c’est-à-dire :
- Soulever l’équivalent d’environ 5kg (16*0.198g + 2 kg pour le préhenseur soit la pince)
- Opérer dans un diamètre d’action > 2 358 mm + 55 mm = 2 413 mm
- Soit un rayon de 1 206.5 mm
Avec toutes ces données, nous avons été en mesure de sélectionner pour une implantation, le robot 3 Série M-10 version iD type 12.
Ai-je acquis la compétence ? |
D’après les critères de la compétence « Développer », j’ai proposé une solution dans un cas simple.
J’ai mis en pratique cette compétence, en résolvant deux problématiques différentes et en présentant des projets conceptuels adaptés aux besoins de chaque client.
J’ai mis au service de notre binôme et du projet les savoir-être suivants :
J’ai fait preuve d’assiduité pour assurer à notre binôme un bon avancement de nos projets et de réactivité quand cela était nécessaire.
D’après tous ces éléments, je pense avoir acquis la compétence « Développer », avec cependant une partie à approfondir, la mise en pratique des deux matières « mécanique » et « dimensionnement des structures ».